
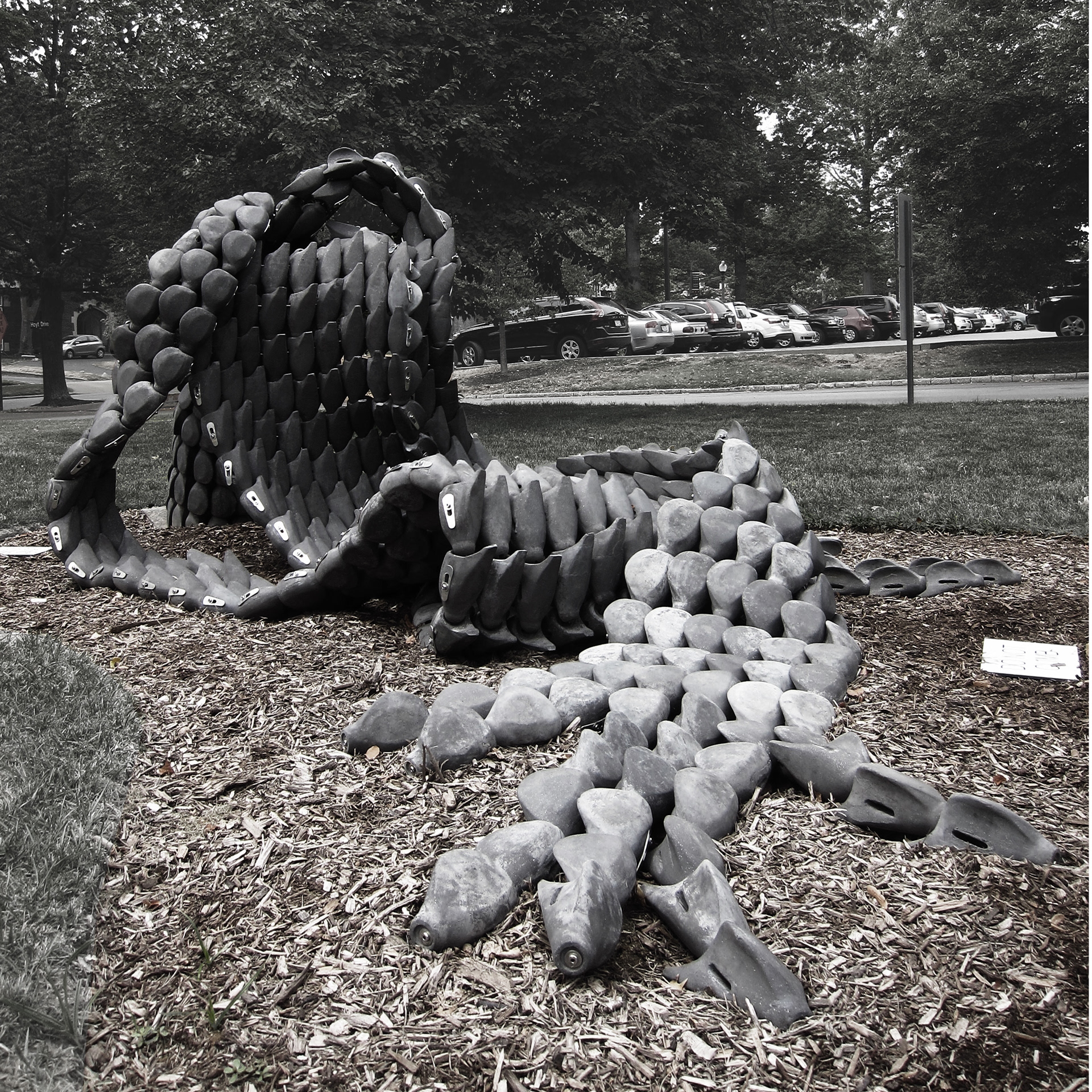
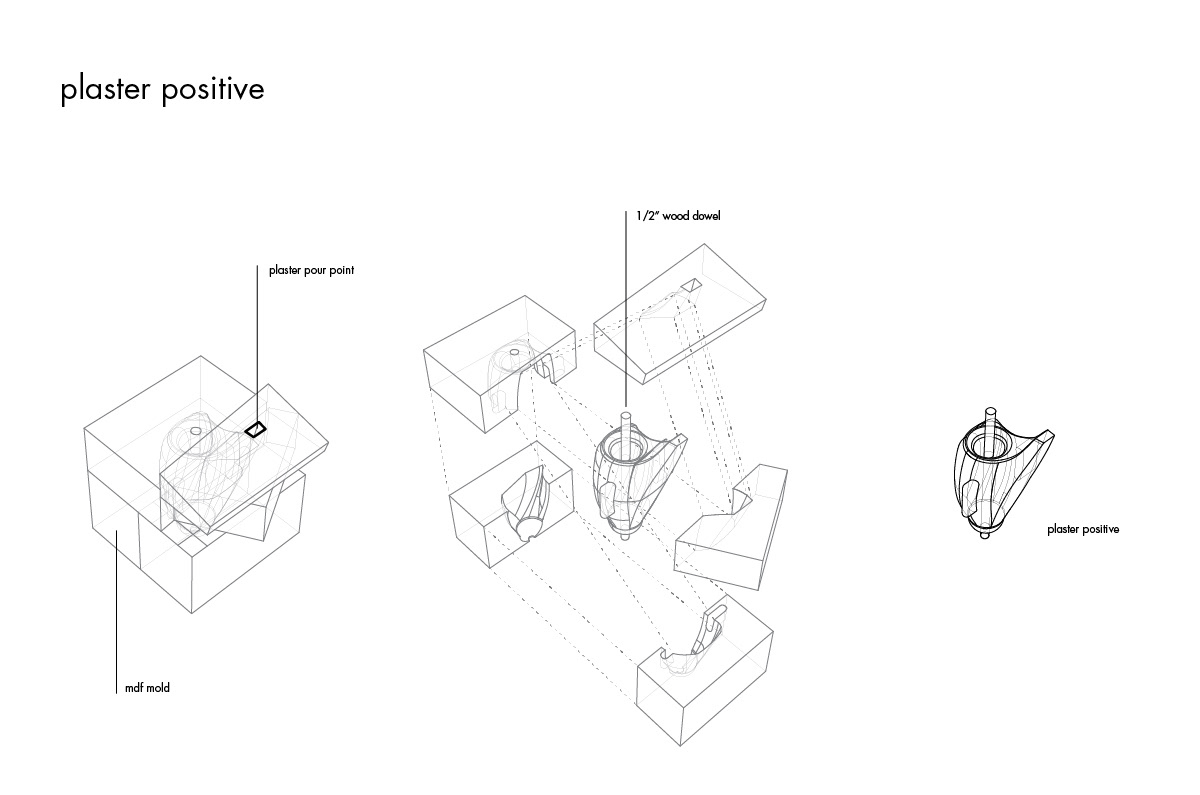
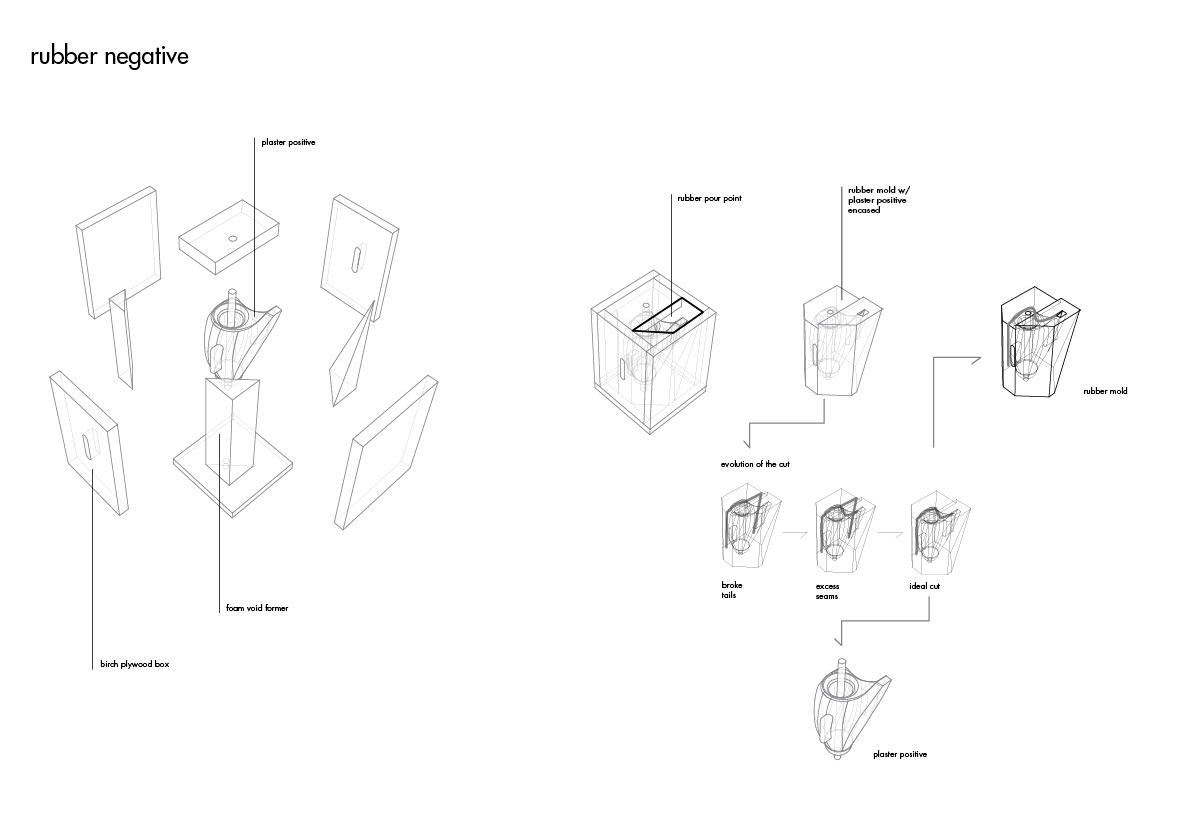
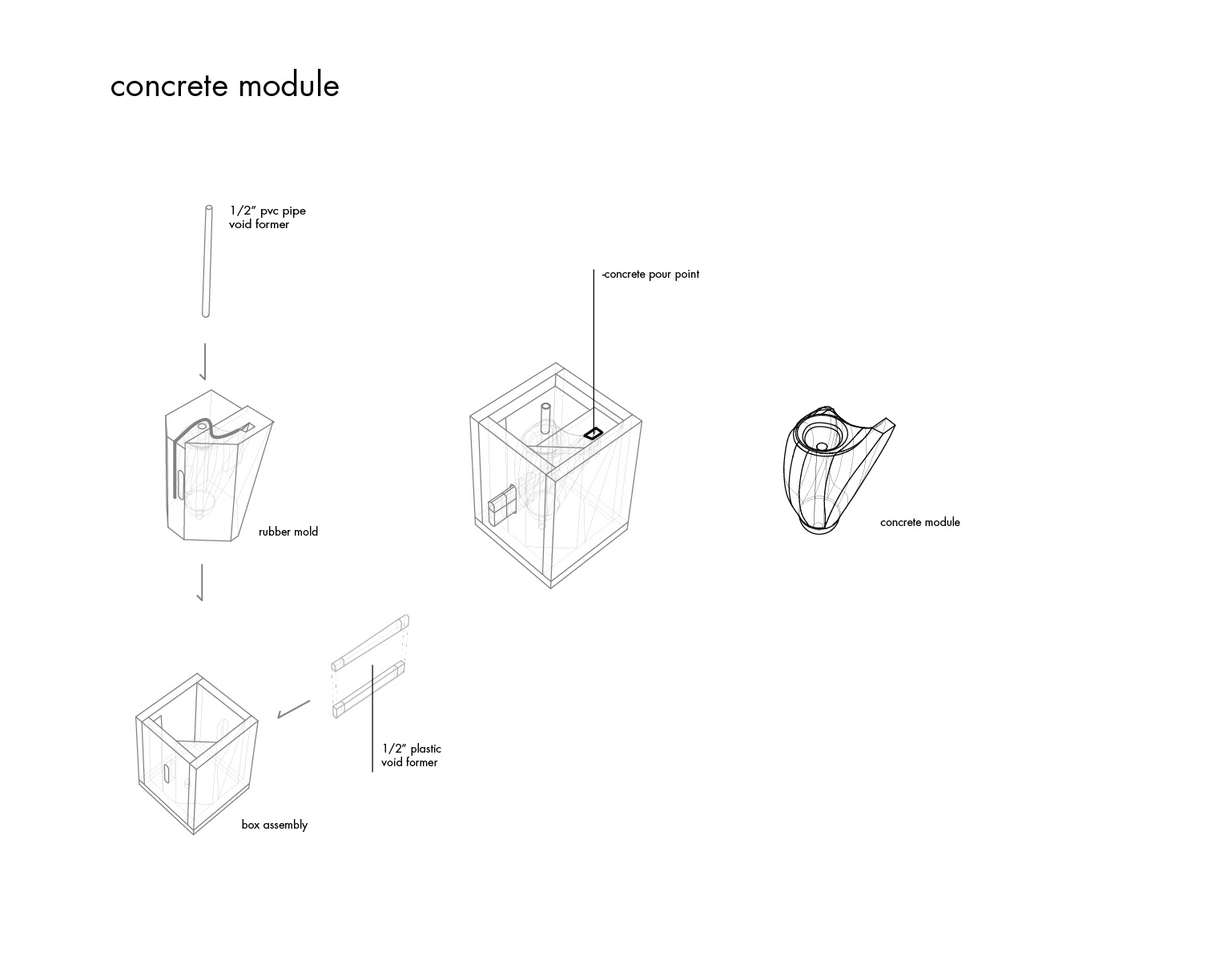


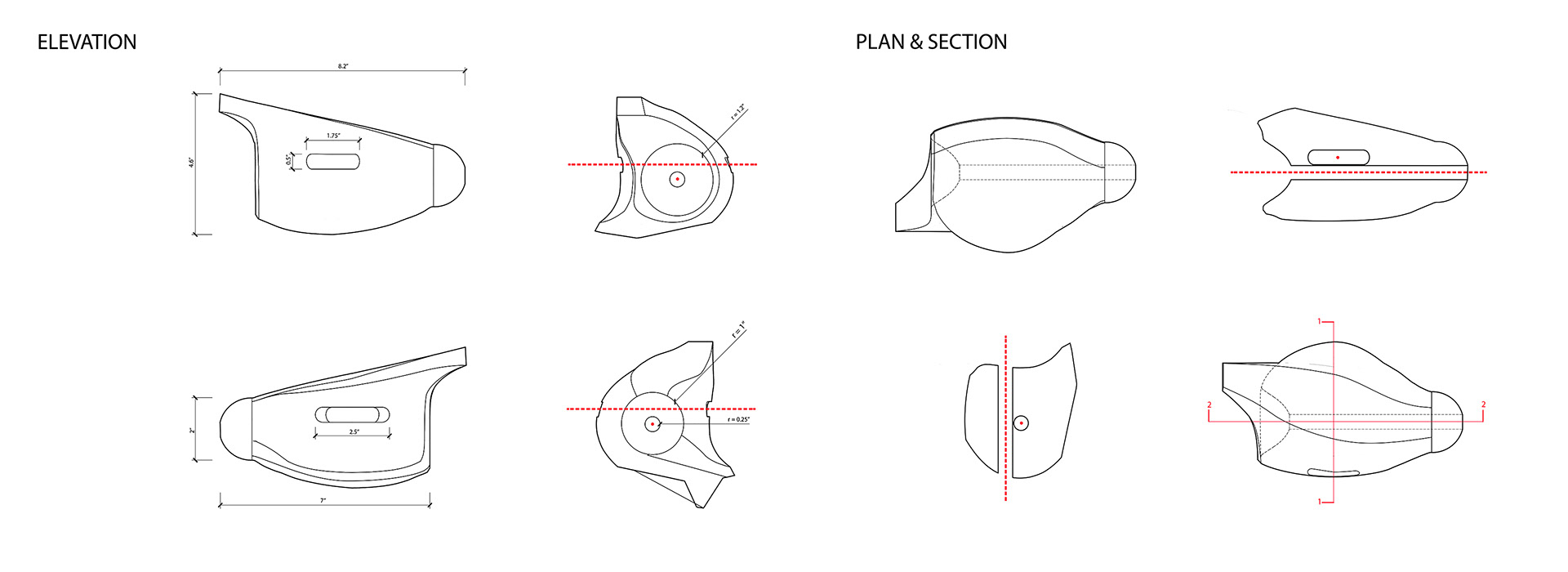
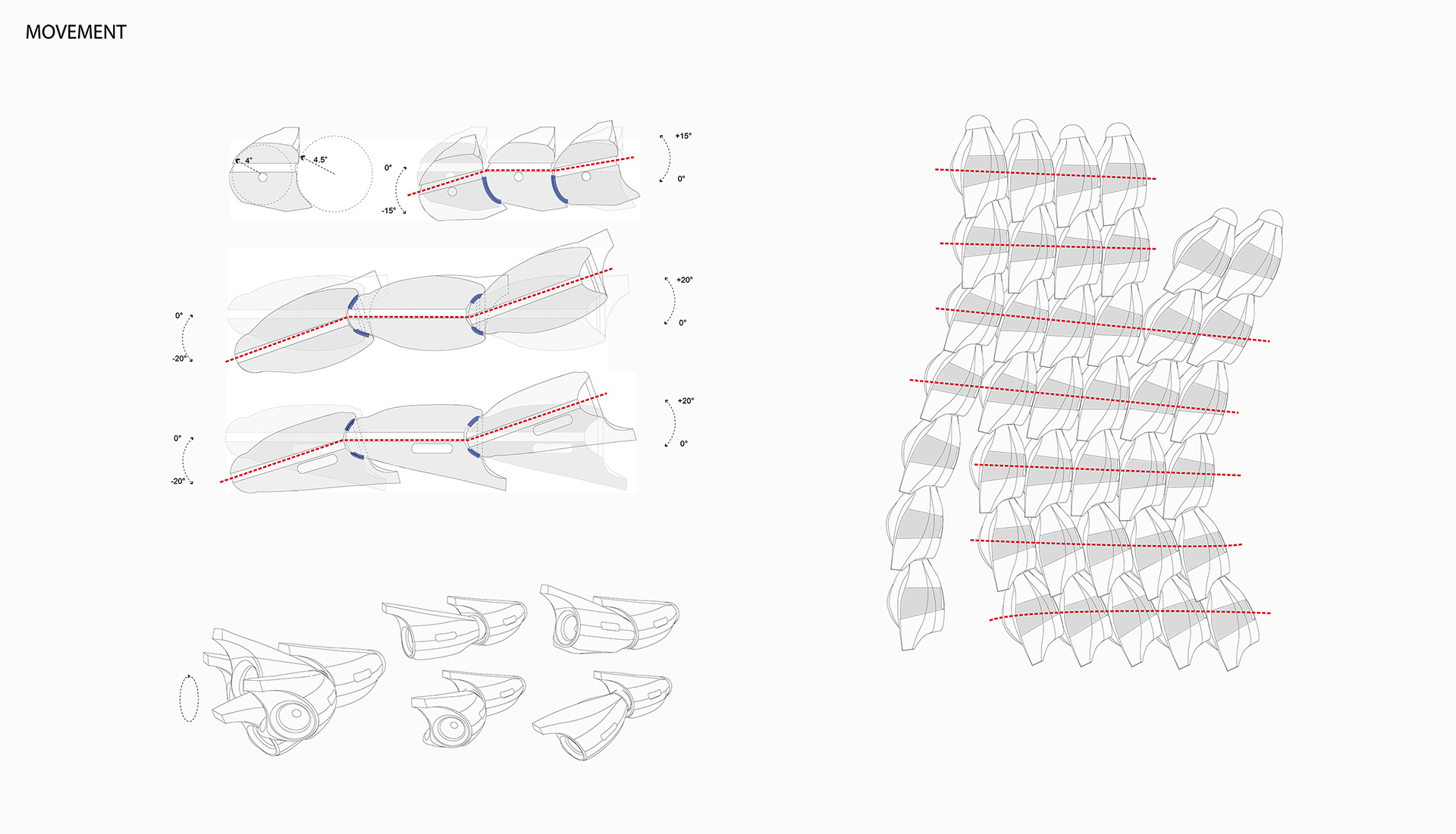
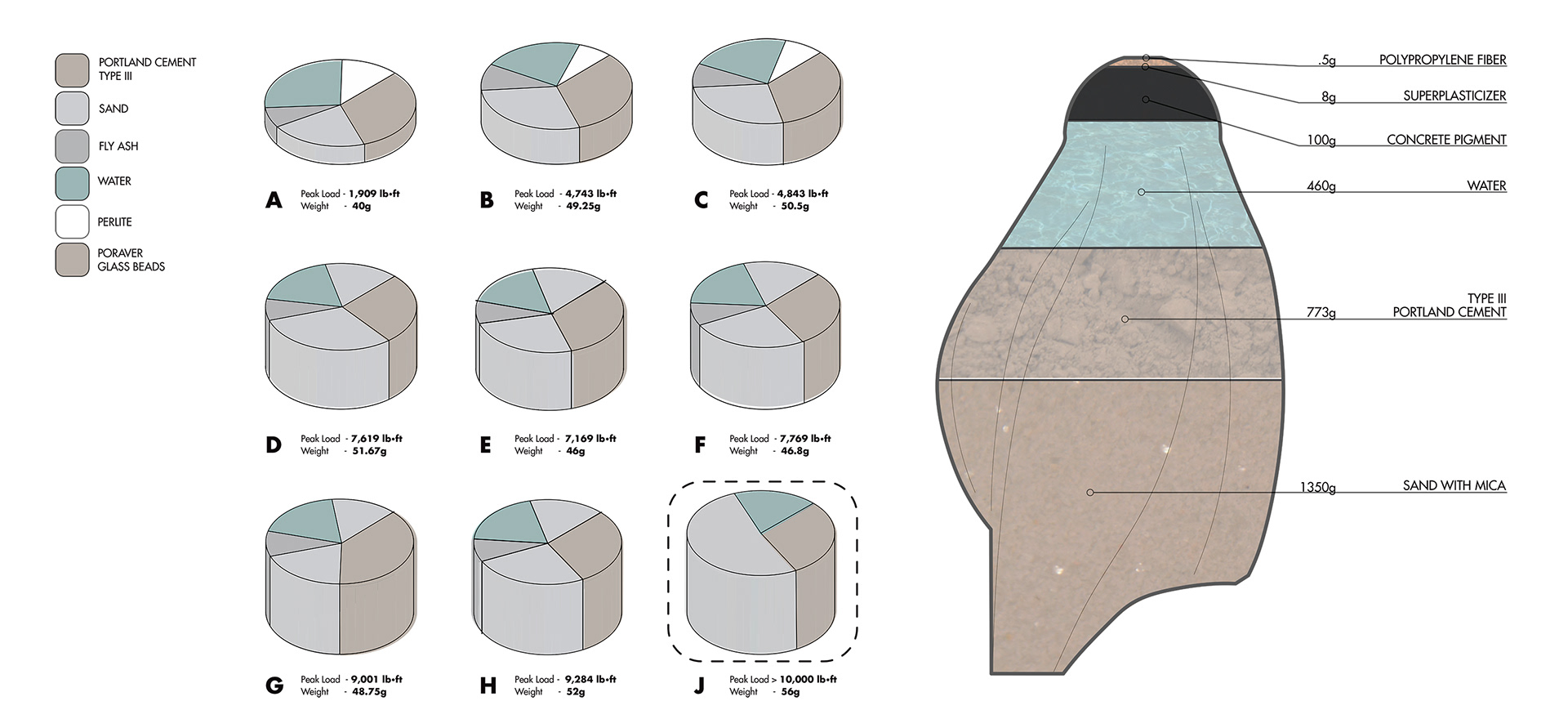

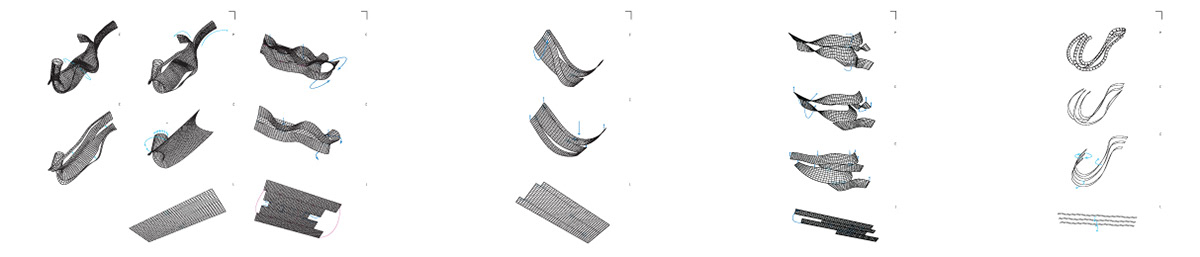
Manis Cementum explores the possibilities of concrete materials and post-tension, compression arch structures. The goal of the studio was to use digital and analog fabrication techniques to create a self-supported sculptural element. Precedents for the project included medieval chain mail, reptilian scales, and various bone structures. The final form takes on an animalistic shape and is therefore given the scientific classification of Manis Cementum. The word "manis" comes from a genus of animals that are covered with large, triangular scales that overlap each other like tiles on a roof. "Cementum" is a play on the Roman word "caementum," which means rough cut stone, and in the case of the Manis Cementum, reflects the nature of the materials being used in the project. The first step in the design process focused on the development of various surfaces and module shapes to find the best technique to use for the full-scale model. By testing different joining strategies and surface manipulations, a working taxonomy of forms and strategies was established. The module itself was carefully designed in order to allow for the greatest range of motion with the fewest number of unique pieces. The final form is comprised of 600 total units with only 3 variations of the unit, making the fabrication of the pieces much simpler. This was important because it allowed for a more standardized and streamlined mold making and concrete casting process, which allowed the studio to stay within its budget and schedule. In addition to the technical and logistical aspects of the module and form, extensive research was done to find the best concrete mixture to use for the final model. Structural testing helped get the concrete with the best strength-to-weight ratio, and a black concrete pigment was added to achieve the desired aesthetic quality. The assembly of the final model used 14 1/4" steel cables in order to accommodate all of the pieces required to create the overall surface design. These main lines were connected together with another set of cross cables, creating a cable-net structure that would hold the surface together. Stainless steel, marine-grade hardware was used to permanently anchor the cables and modules in place. Because of the size and weight of the final model, a construction phasing system had to be designed. The project was broken up into separate elements, allowing for a more organized and sequential construction process. The final model is sited on the western side of the architecture school at Washington University in St. Louis. It is specifically oriented to provide the best views to visitors approaching the building from all angles. This digital fabrication studio was a collaborative effort with the following individuals: Michael Chung, Guru Liu, Ruogu Liu, Lu Bai, Christopher Quinlan, Enrique de Solo, Shuang Jiang, Christopher Moy, David Turner, and Zhe Sun.