Robotically manipulated façade components
This research proposes a new design and manufacturing methodology for architectural ceramics that leverage both heterogeneities and mass production capable of supporting variation in bespoke façade components at the building scale.
What material affects emerge when robotic manipulation of clay exceeds the layer-based methods of 3D printing? Are the imprints of robotic tooling different than that of the human hand? In this project, we pushed robotic 3D printing to its limits and developed two novel means of fabrication: 3D printing clay on three-dimensional objects in free space and robotic manipulation of clay in the plastic body stage.
GENERATIVE DESIGN METHOD
From a design perspective, our project was influenced by two critical materials and formal desires. The first was to be self-supporting, and therefore a volumetric approach was required. The second was to be porous as an assembly, allowing for light to pass through the façade. This desire was focused after discovering the jumping cholla, a cactus with multi-scalar material organization across the body to create both stiffness and porosity
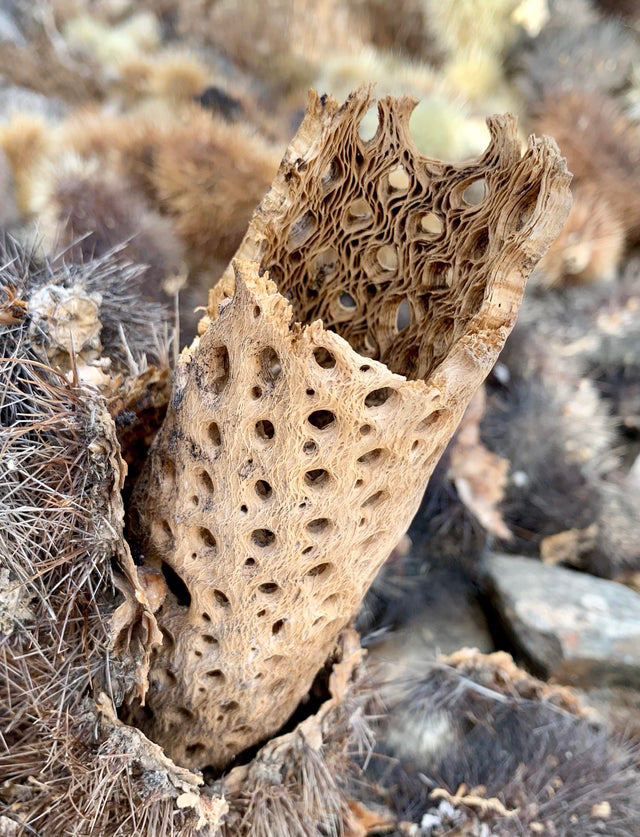
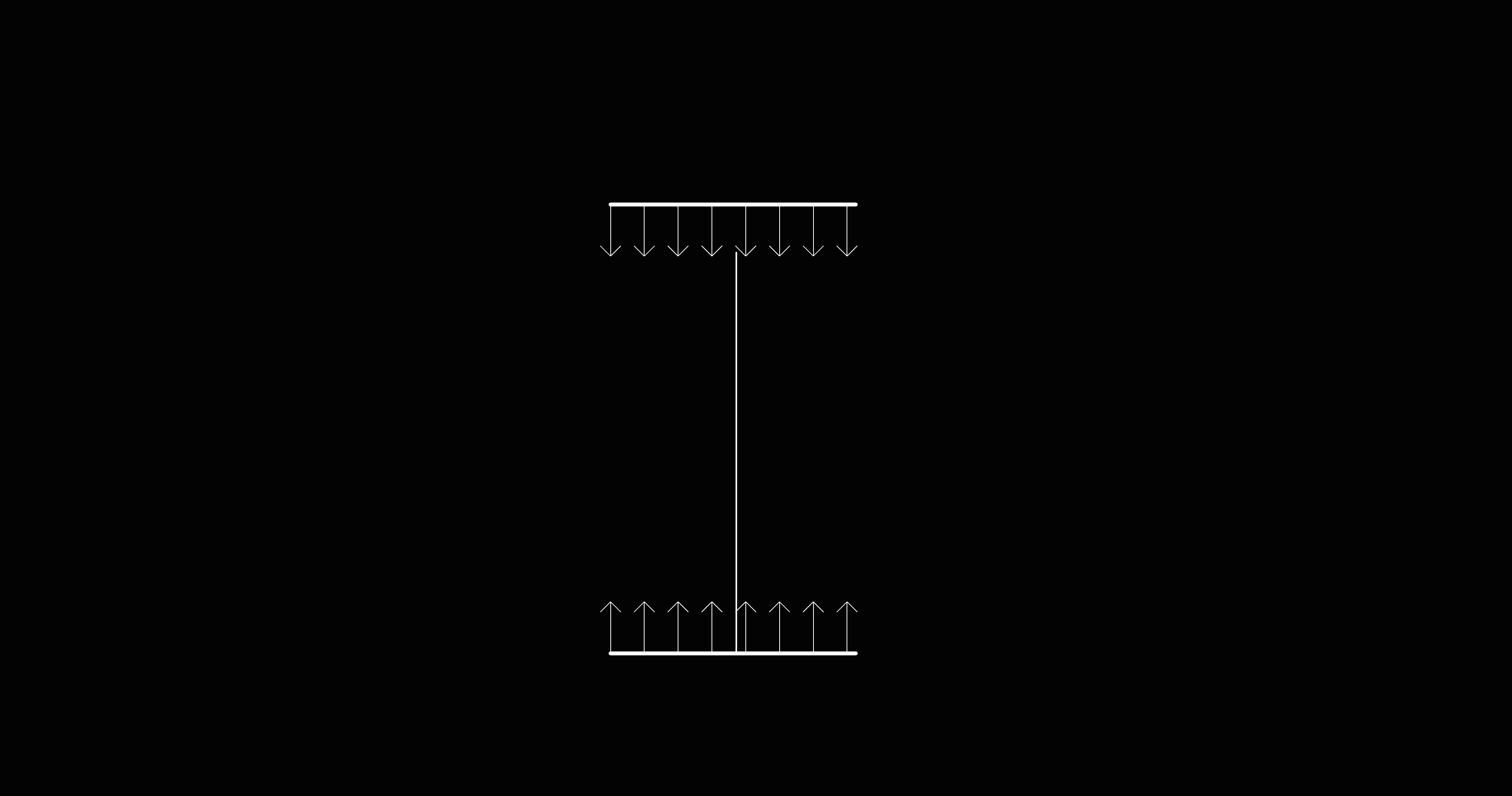
COMPUTATIONAL TOOLS
In order to enable the development of complex ceramic forms and ornament we had to research and create complex computational tools. What follows are visual representations of design algorithms, generative studies into material placement, and robot control processes which opened up new avenues of exploration within the confines of our lab environment.
AGENT CATALOGUE 1
Early development of robotic path control was initiated through agent steering behaviors based on Craig Reynolds seminal work. These agent paths begin to develop a tailorable and responsive robotic pathing towards the development of a new architectural ornament.
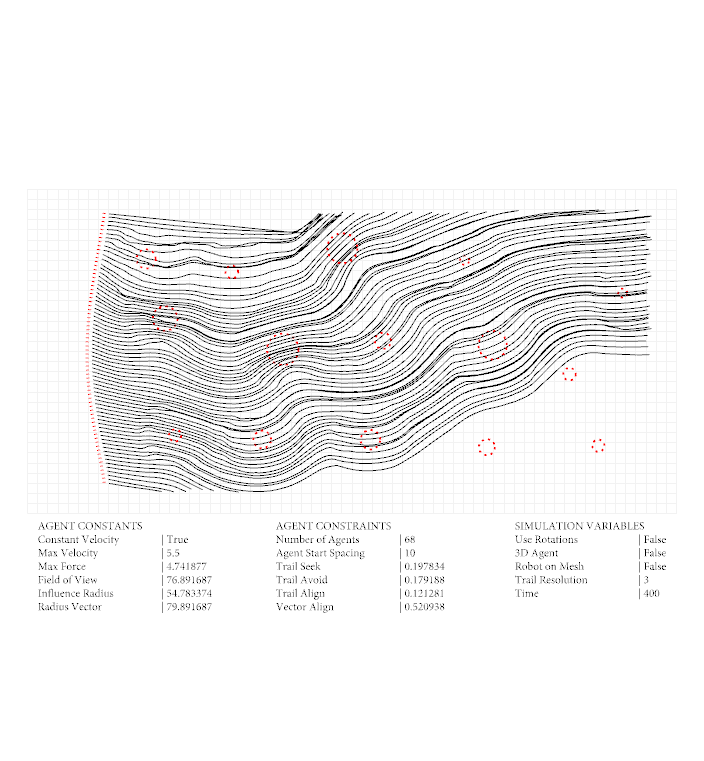
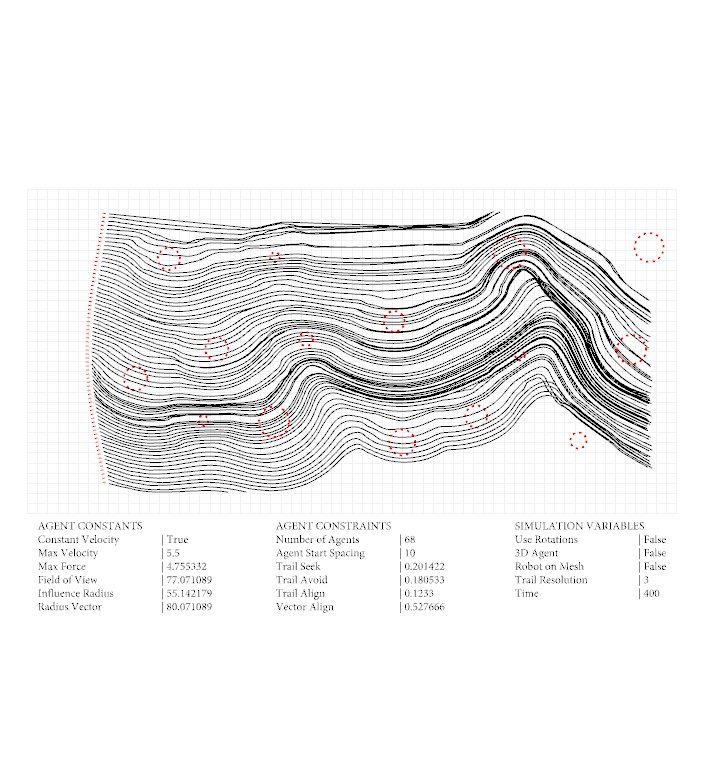
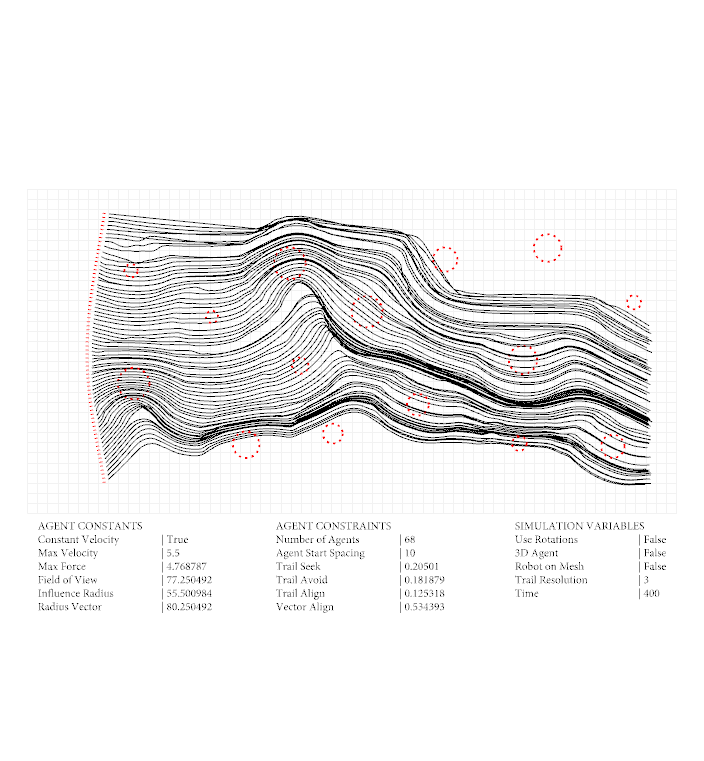
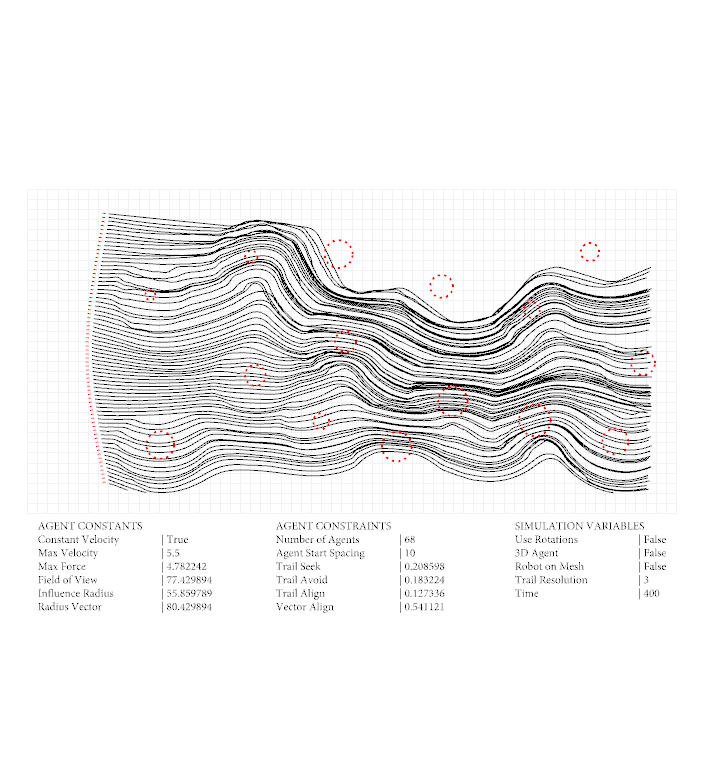
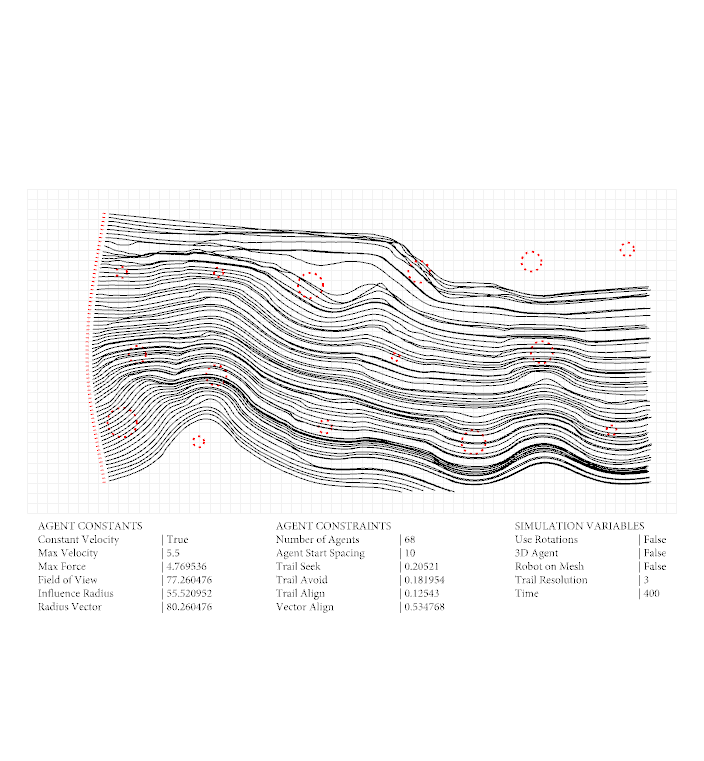
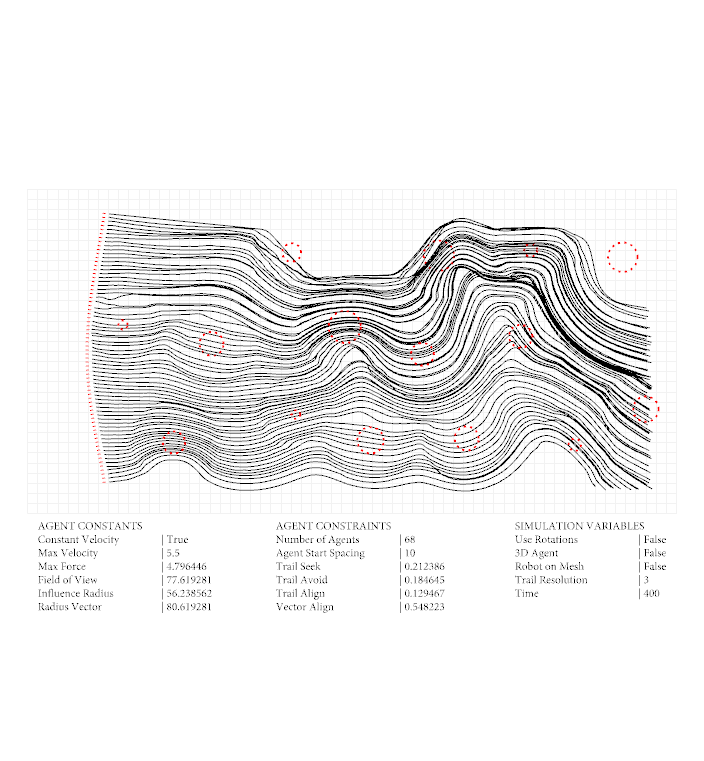
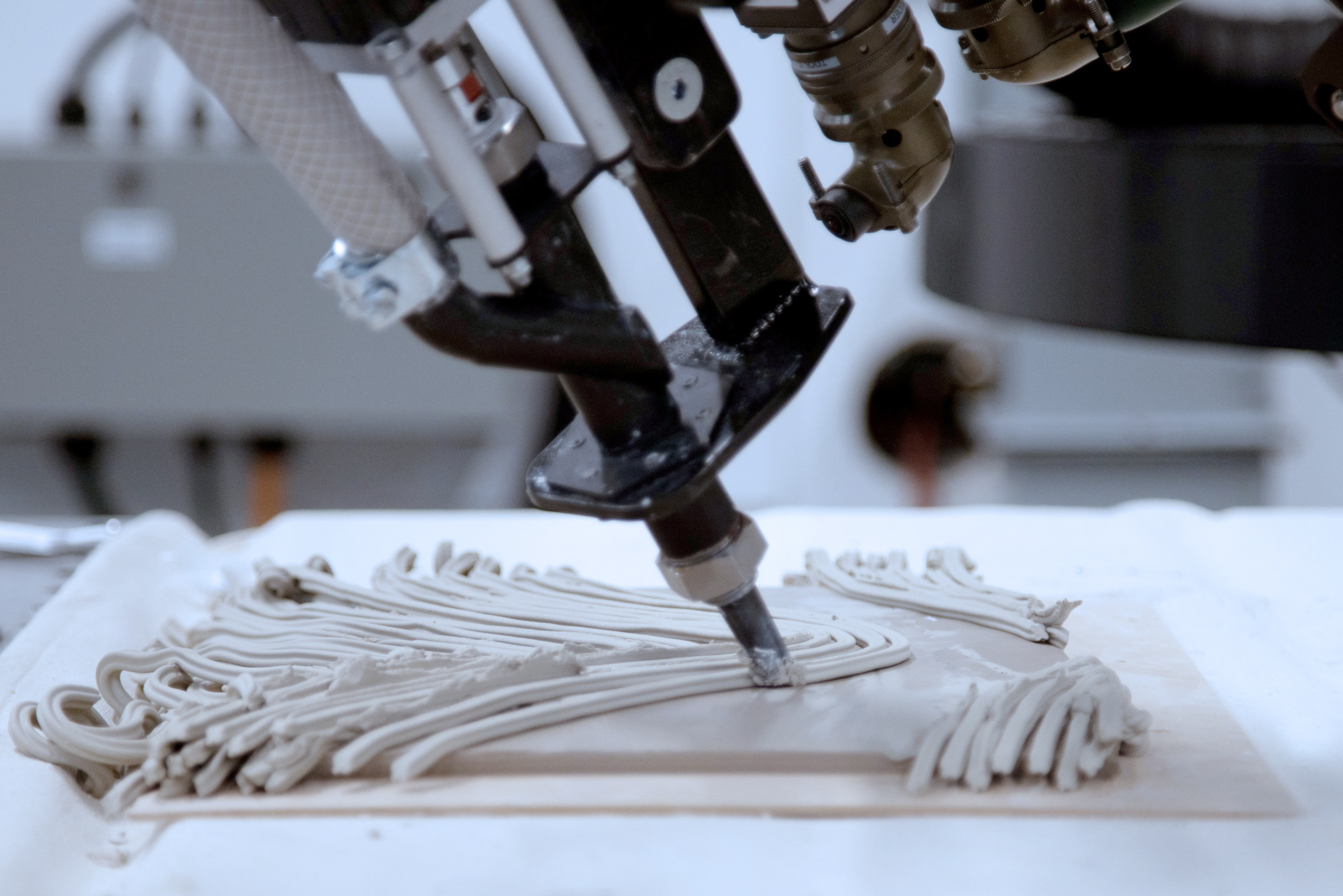
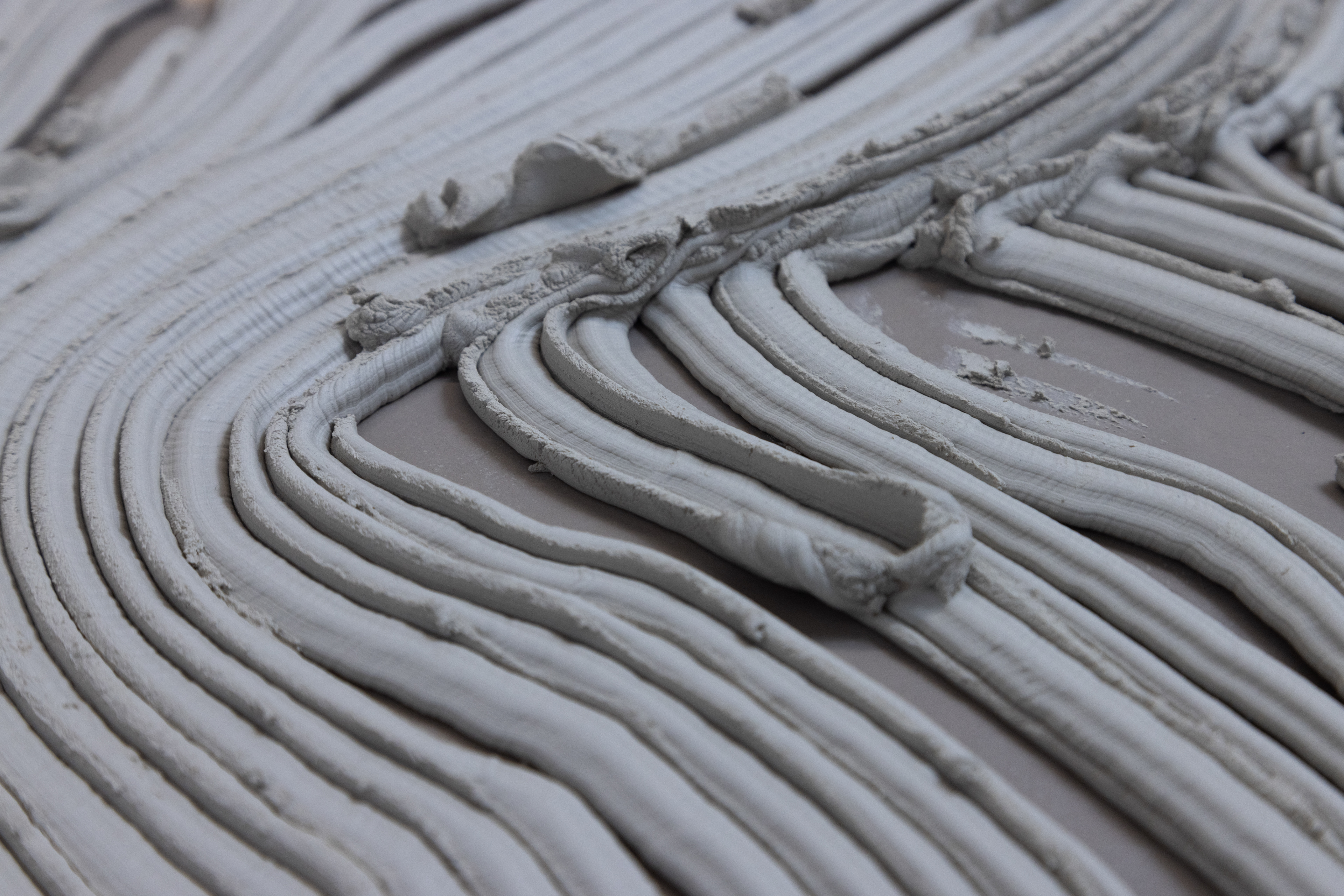
AGENT CATALOGUE 02
Behaviors were then applied to these initial paths in a secondary process, further modifying and developing the paths.
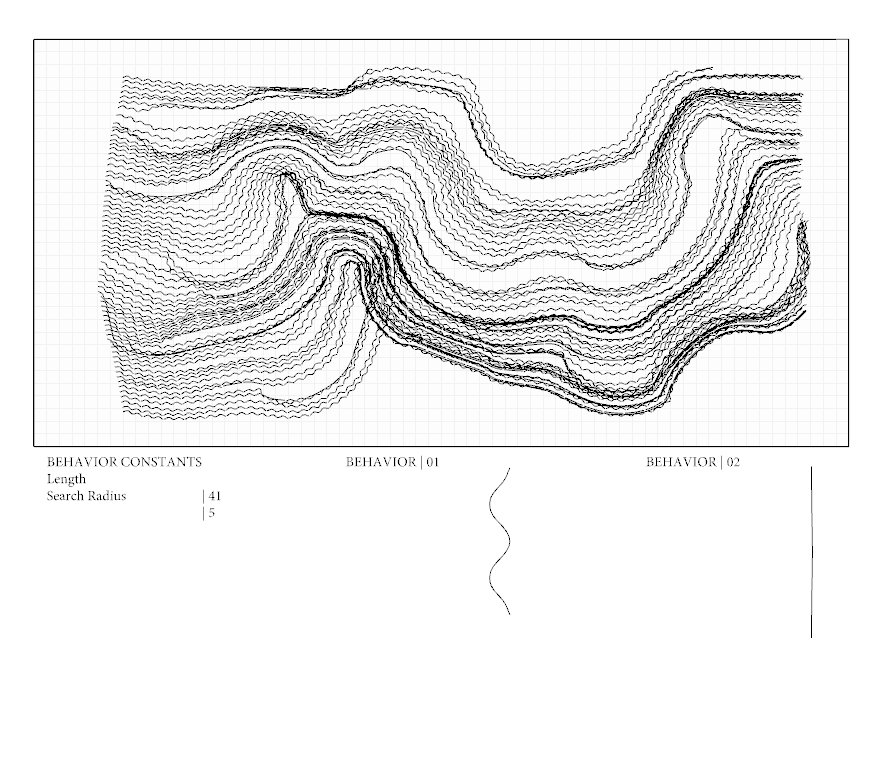
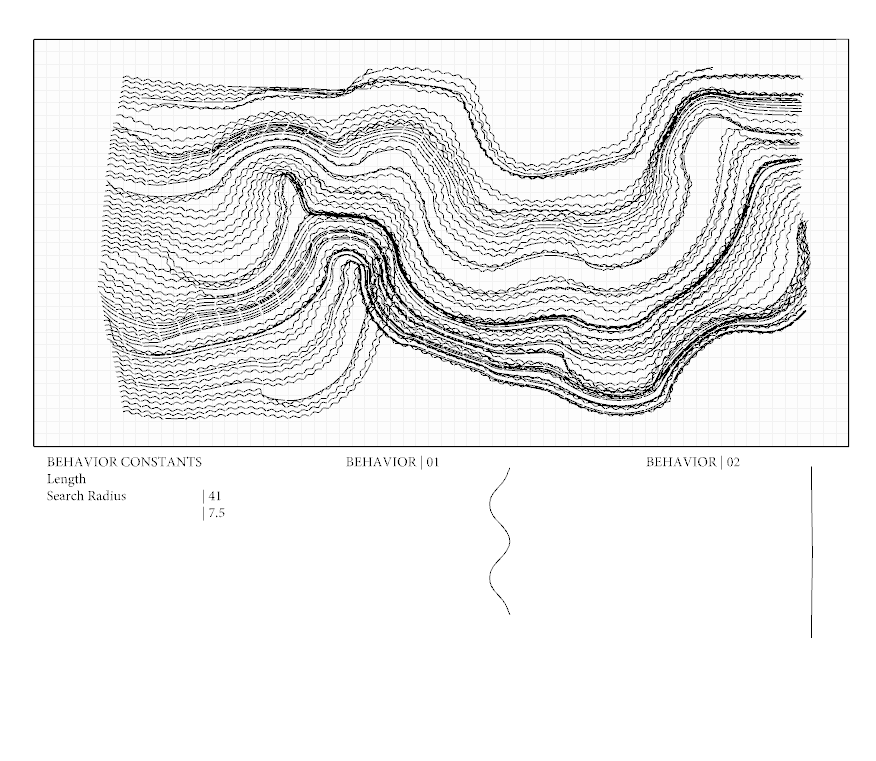
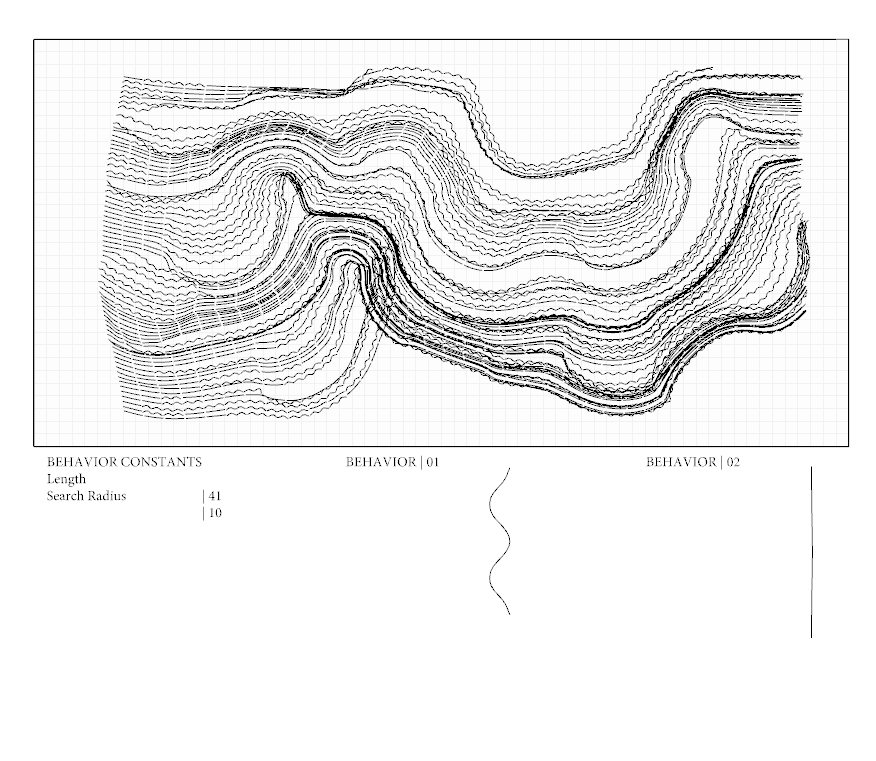
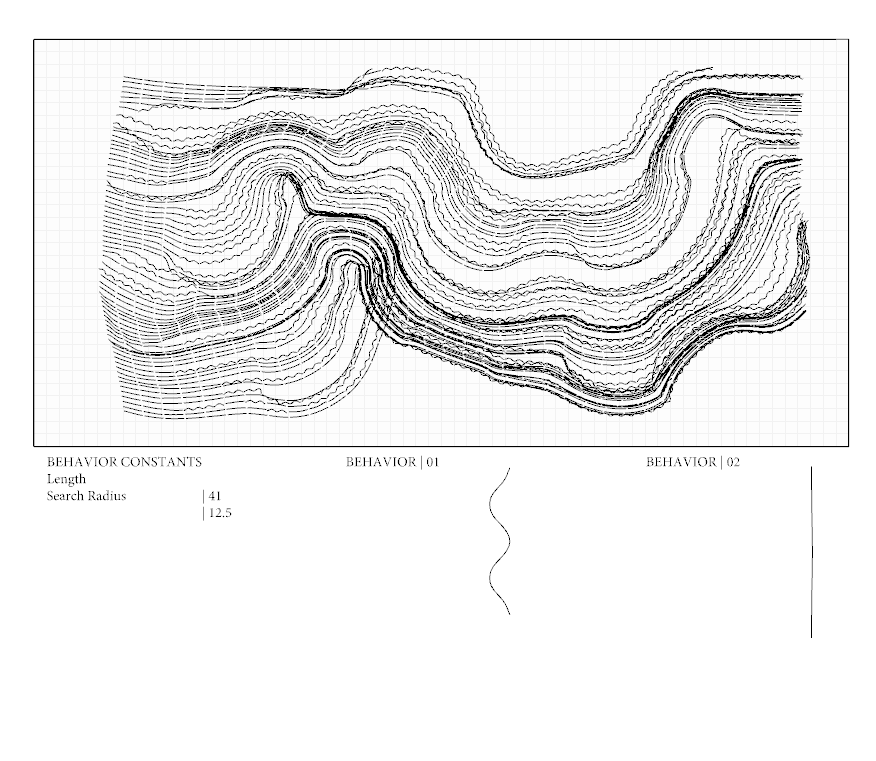
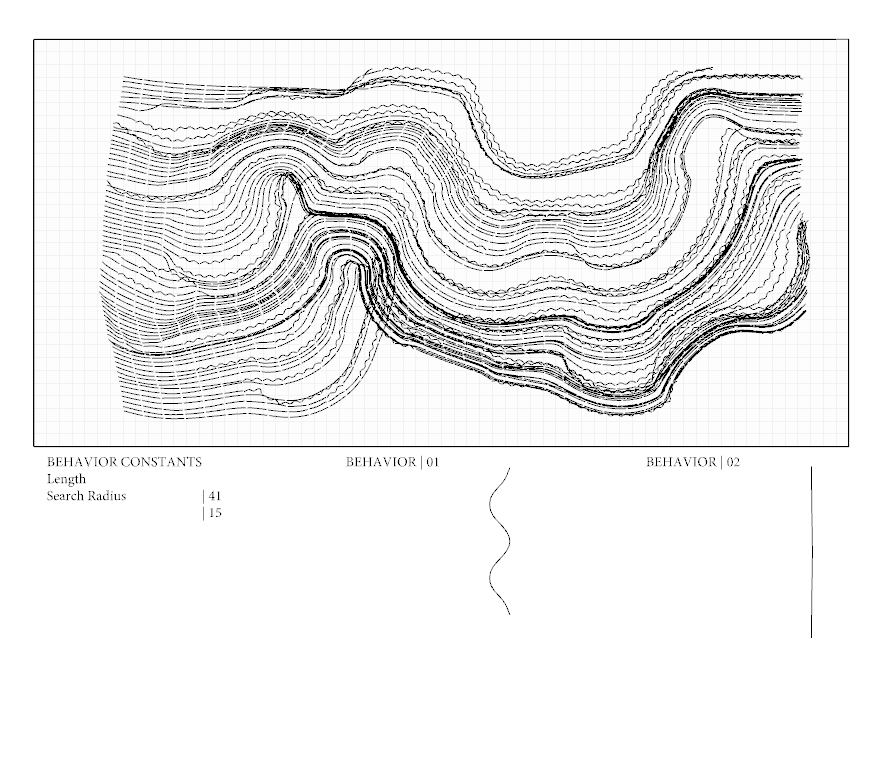
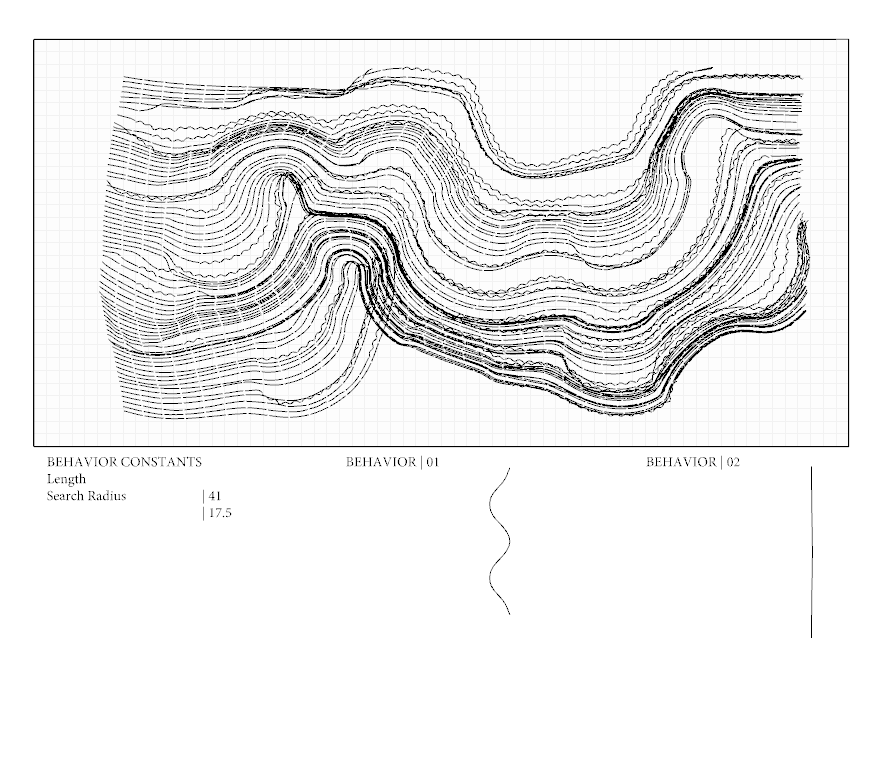
TOPOLOGICAL SHAPE OPTIMIZATION
We implemented a TSO (Topological Shape Optimization) modeling system as a generative design tool to explore how material might be organized along a laminar surface.
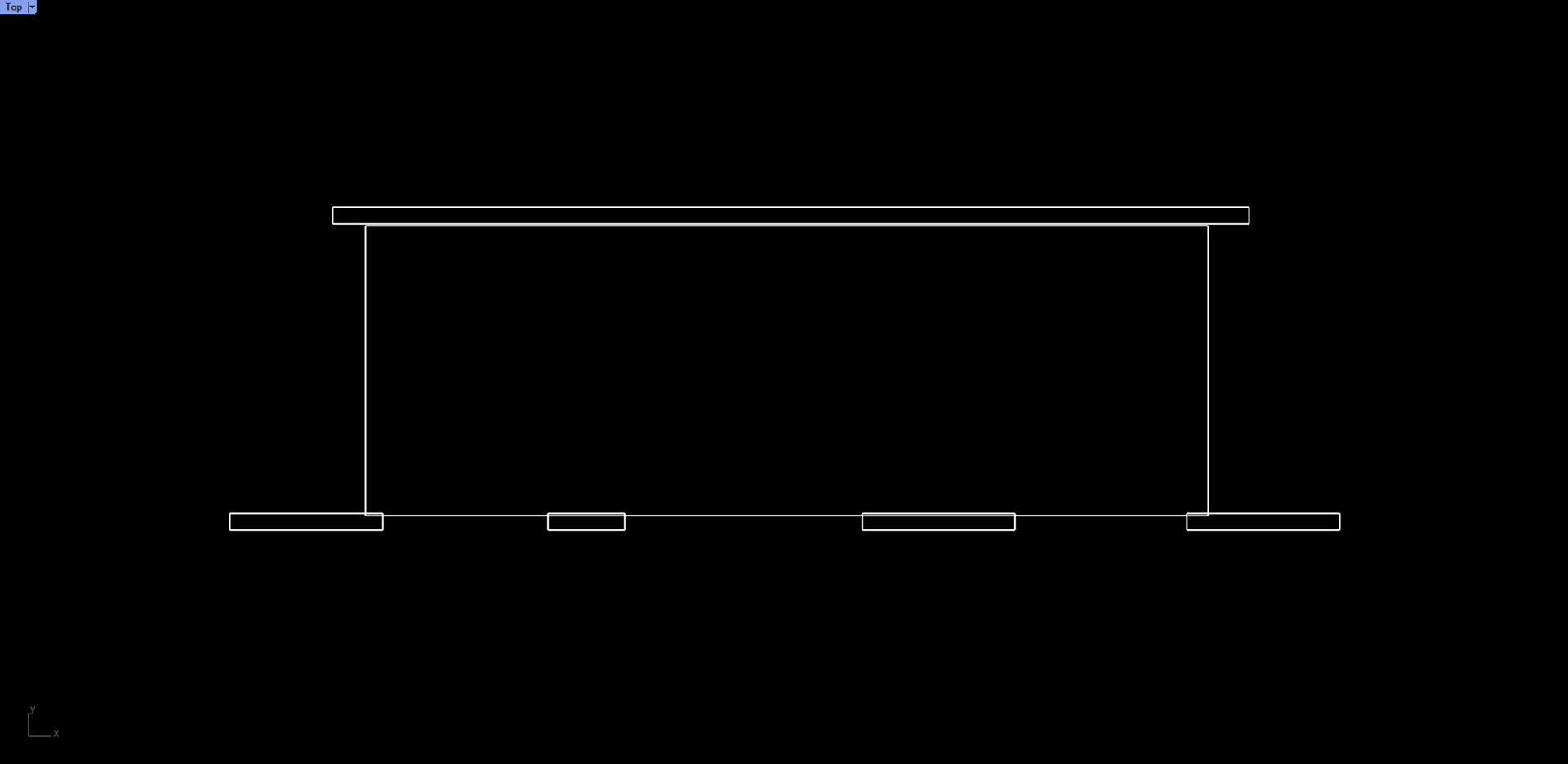
base boundry

aperture mapping
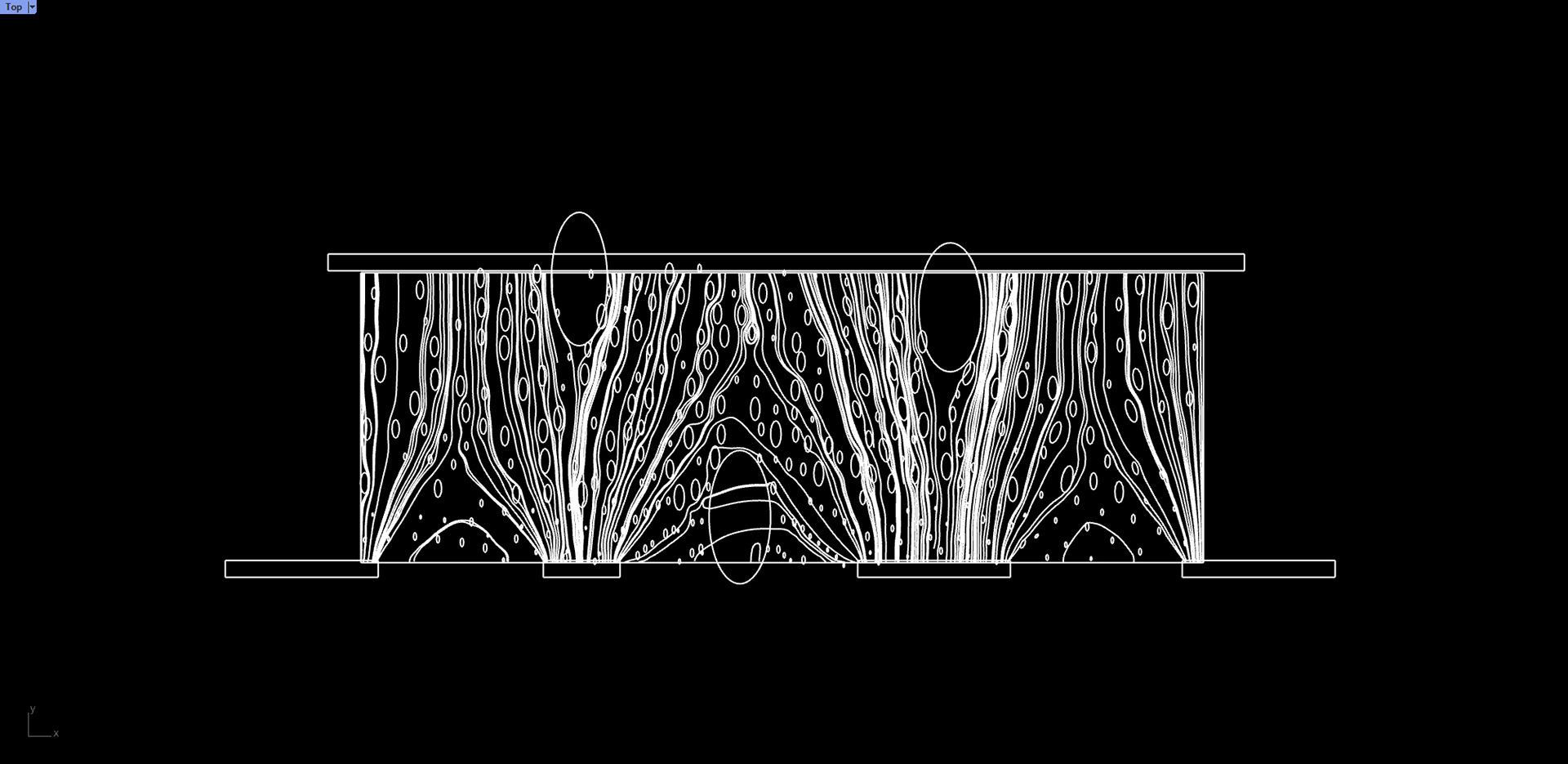
TSO analysis
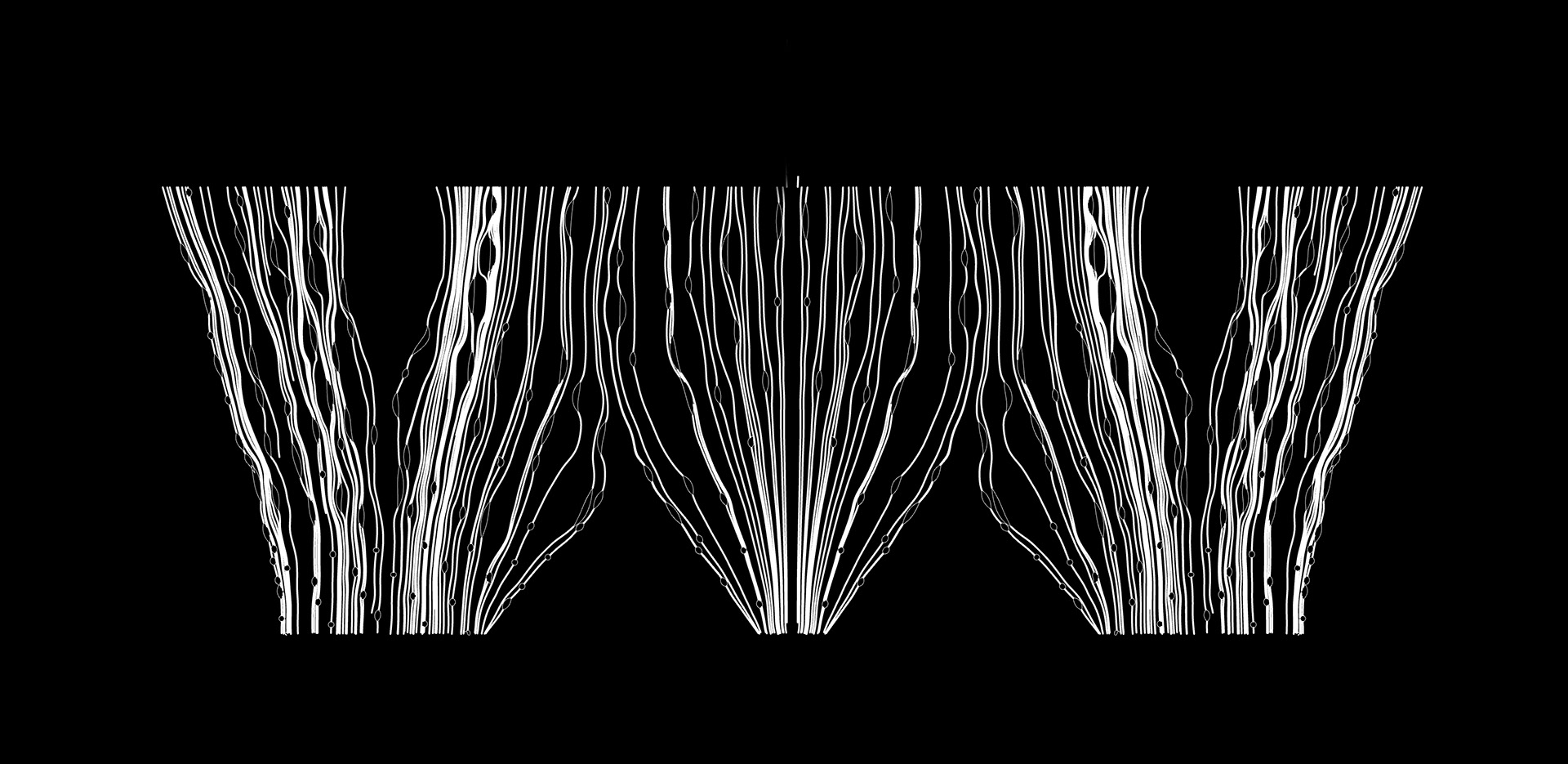
TSO stress curves

PARTICLE PHYSICS SIMULATION
Houdini particle simulations play out to orient material along the curves and develop a delaminatory approach to volume modeling.
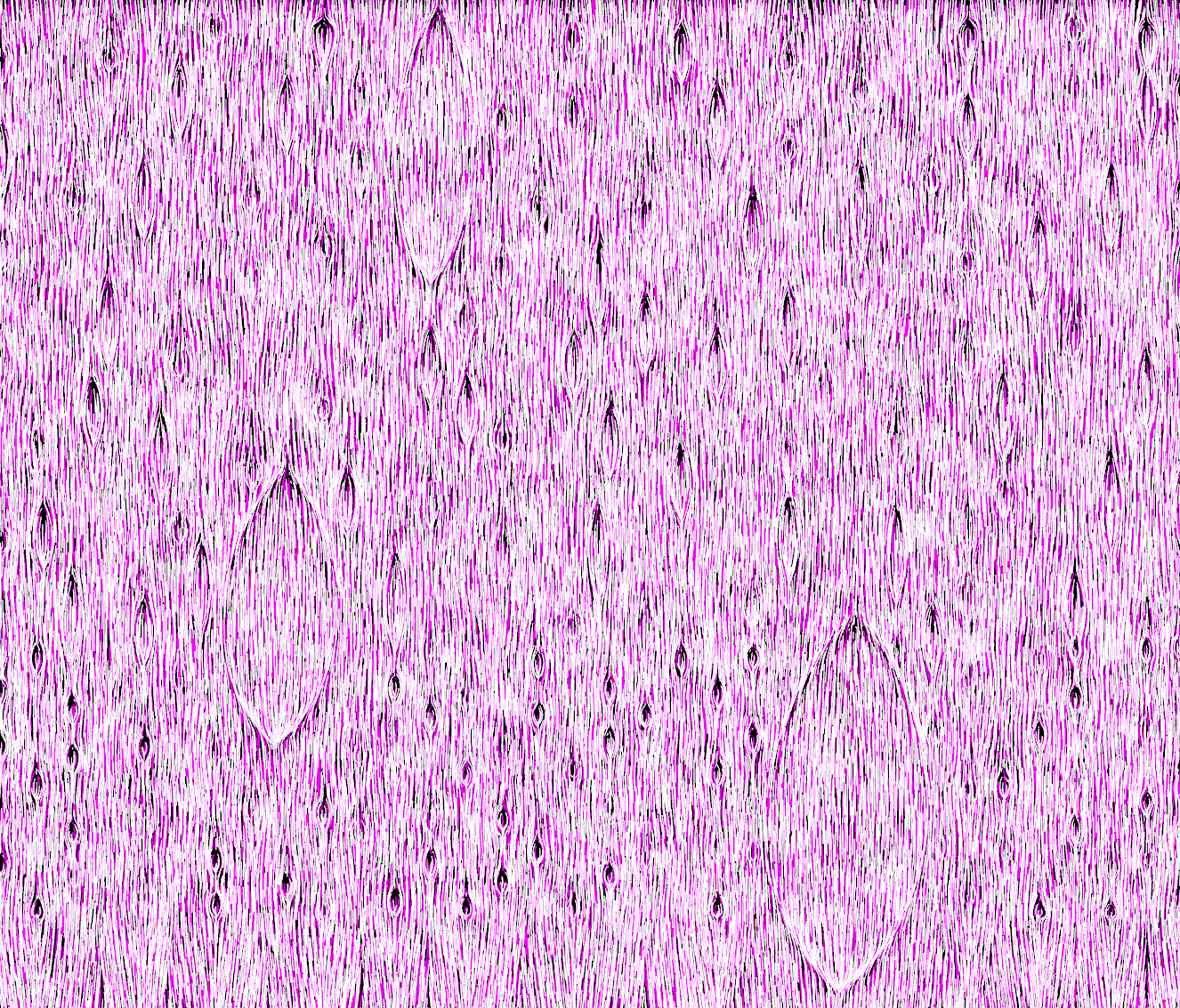
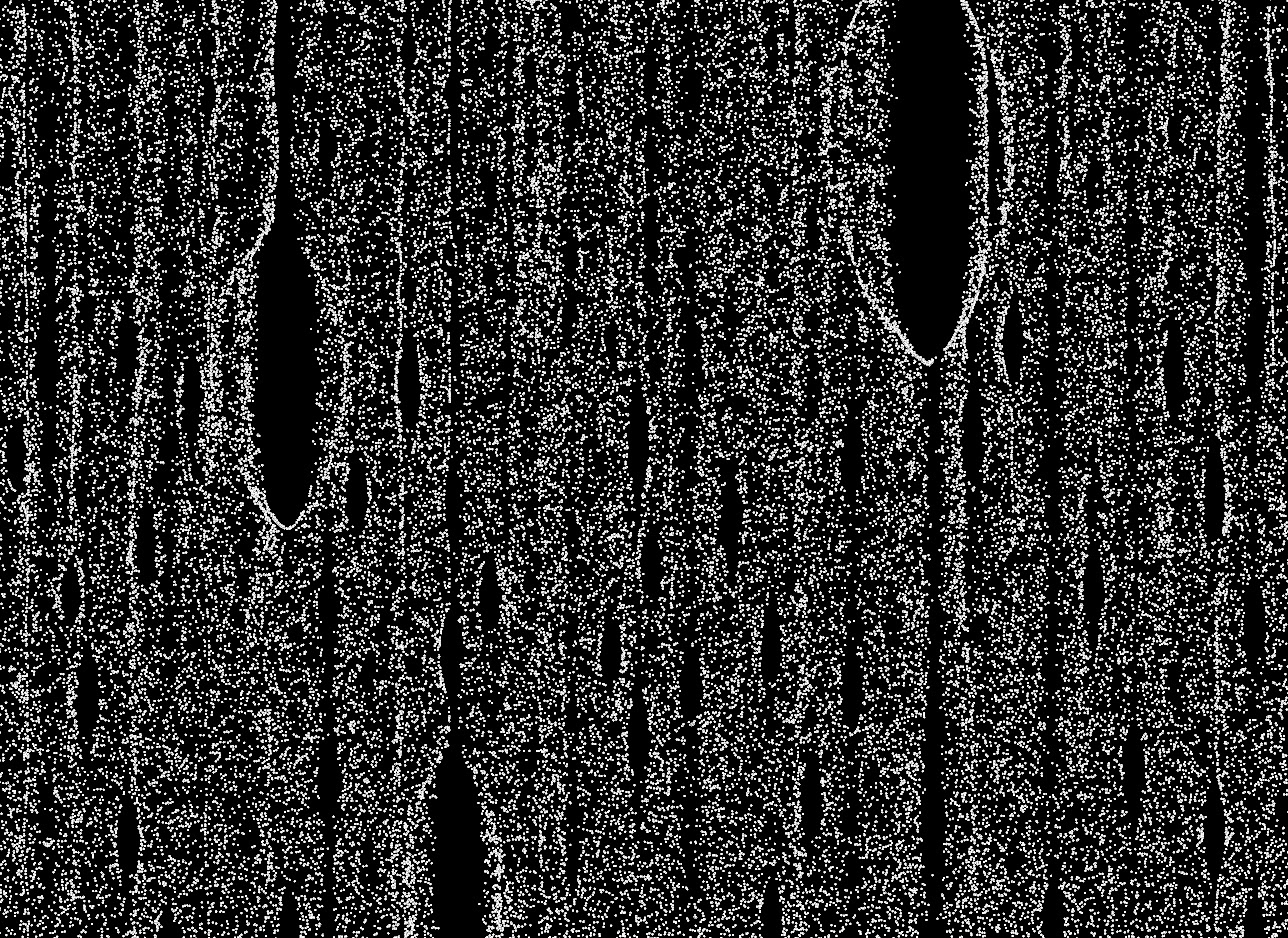
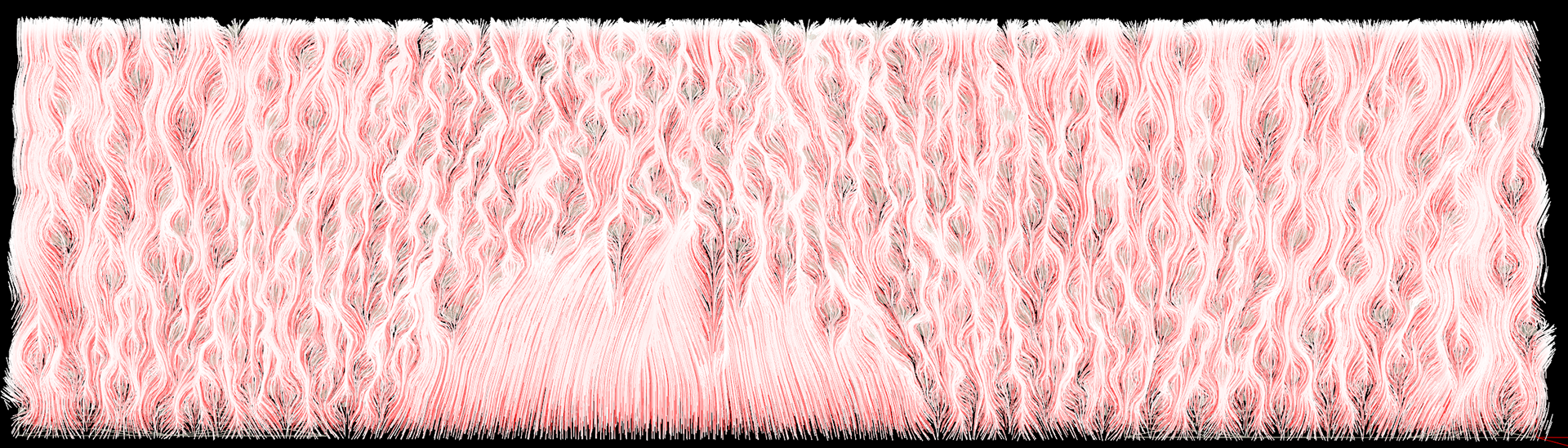
BUILDING FACADE PROPOSAL
A building proposal was established in order to extend our research and consider the greater architectural implications of our mock-up design as we developed it. This proposal provided opportunity to push back on the mock-up with how it performed as an architectural façade system, both as an object of scale and materiality, but also at a multi-scalar level, with how ornament established itself throughout the work.
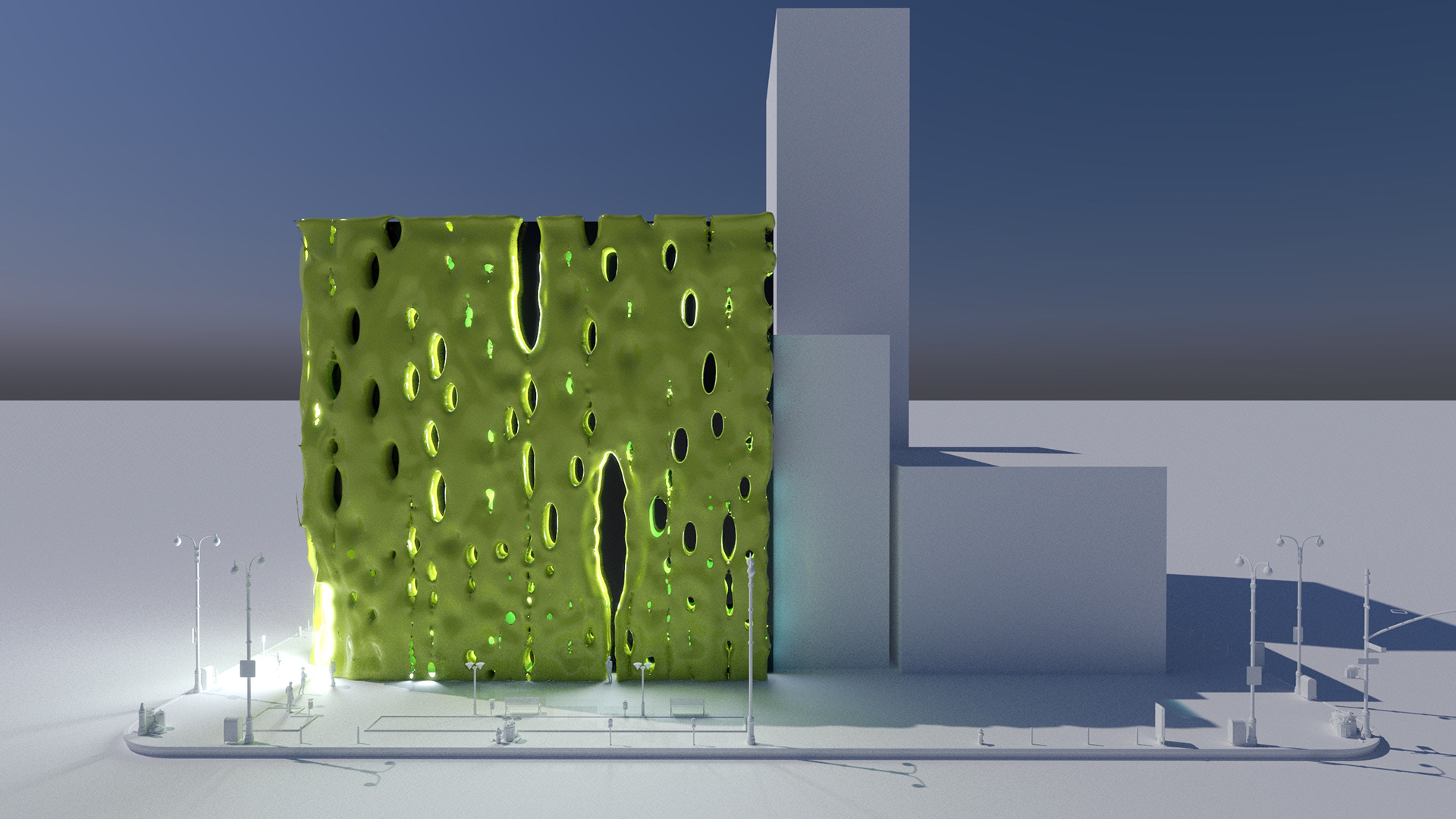
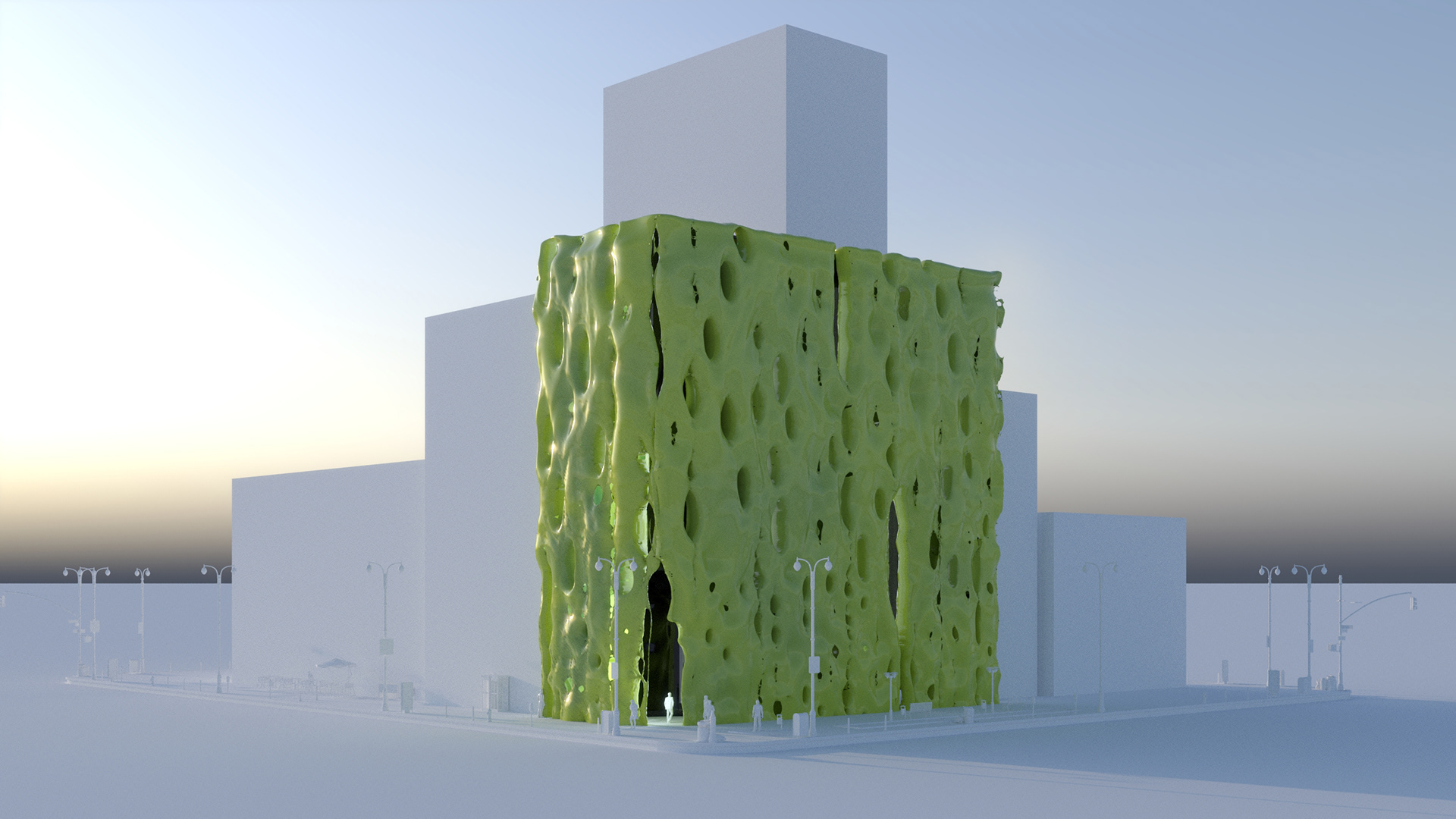
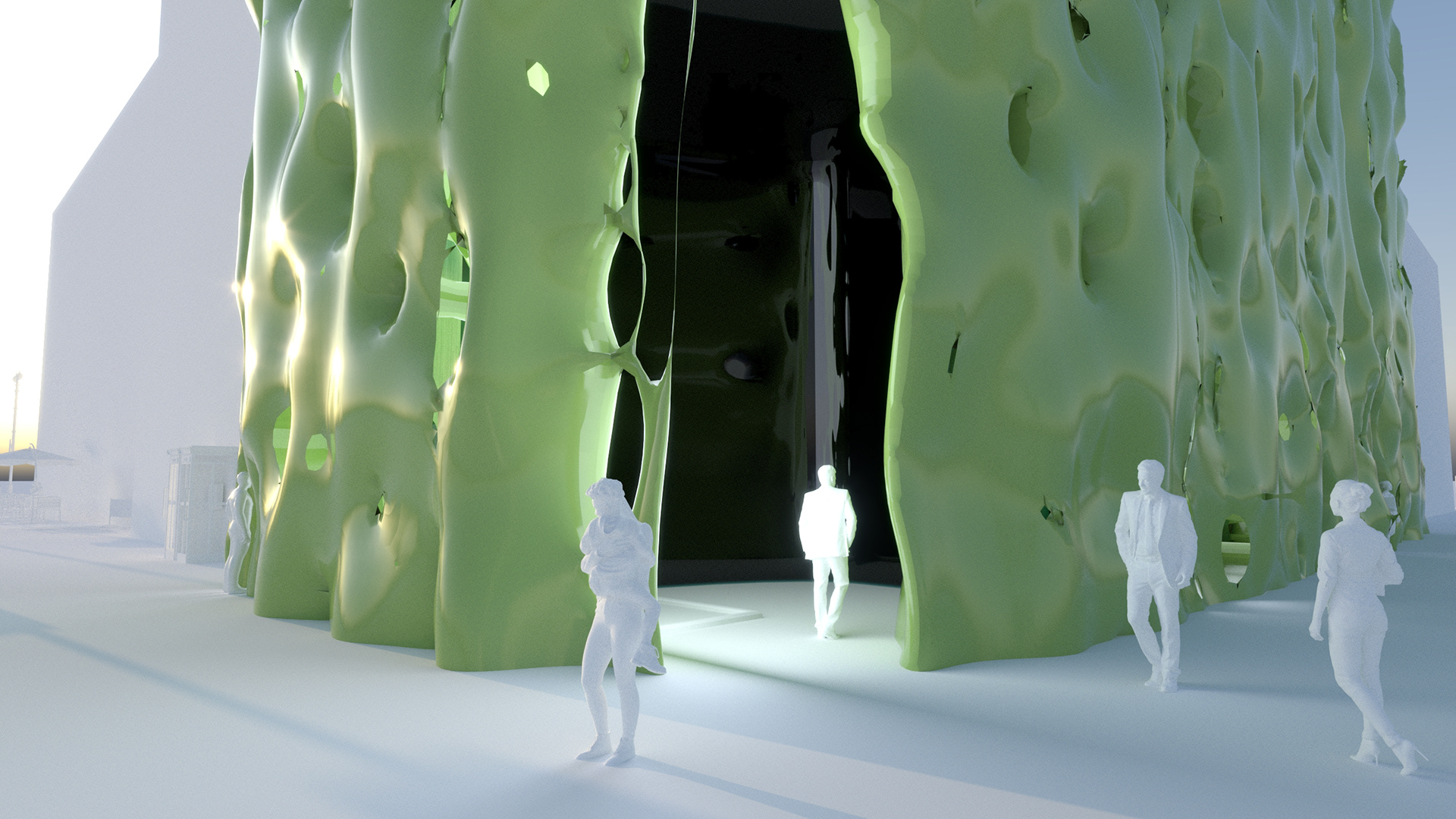
PRODUCTION PROCESS
Digital Tools (VR/AR)
Robot collisions with the pre-existing geometry was a primary issue as we began to develop a multi-step robotic process. As the image at right shows, the robot peripheral equipment was often a burden in developing 6-Axis extrusion and manipulation paths. Although simulation and collision management was used within our path-planning framework, we wanted to begin research into how a human interface might allow for more adept control of individual robot orientations within a larger operation.
To overcome these challenges, we proposed a real-time monitoring system which would enable a robot operator to isolate potential upcoming collisions points along a robot path and then send those areas to a human mediator for manipulation. Using a VR rig, the mediator could then manipulate a localized set of points dynamically, unencumbered from the 2-Dimensional and limited perspective of a standard CAD/CAM system.
`6-Axis industrial robotic arms are often considered to be largely anthropomorphic machines; their motions can be understood through an embodiment of the machine itself. When attempting to explain or understand robotic motions, users will use their own bodies, arms, and hands to mimic rotations and plane orientations. However, the development and simulation of robotic path-planning is still an un-embodied process, often relying on computer aided design (CAD), computer aided manufacturing (CAM) software interfaces, and computer screens to develop and simulate the robot processes. This paper presents an offline method for editing and simulating robot motion paths in a virtual reality (VR) environment using hand control to directly edit robot target planes. This approach is especially relevant in the modification of complex one-off robotic programs commonly used in advanced robotic fabrication of unique objects.
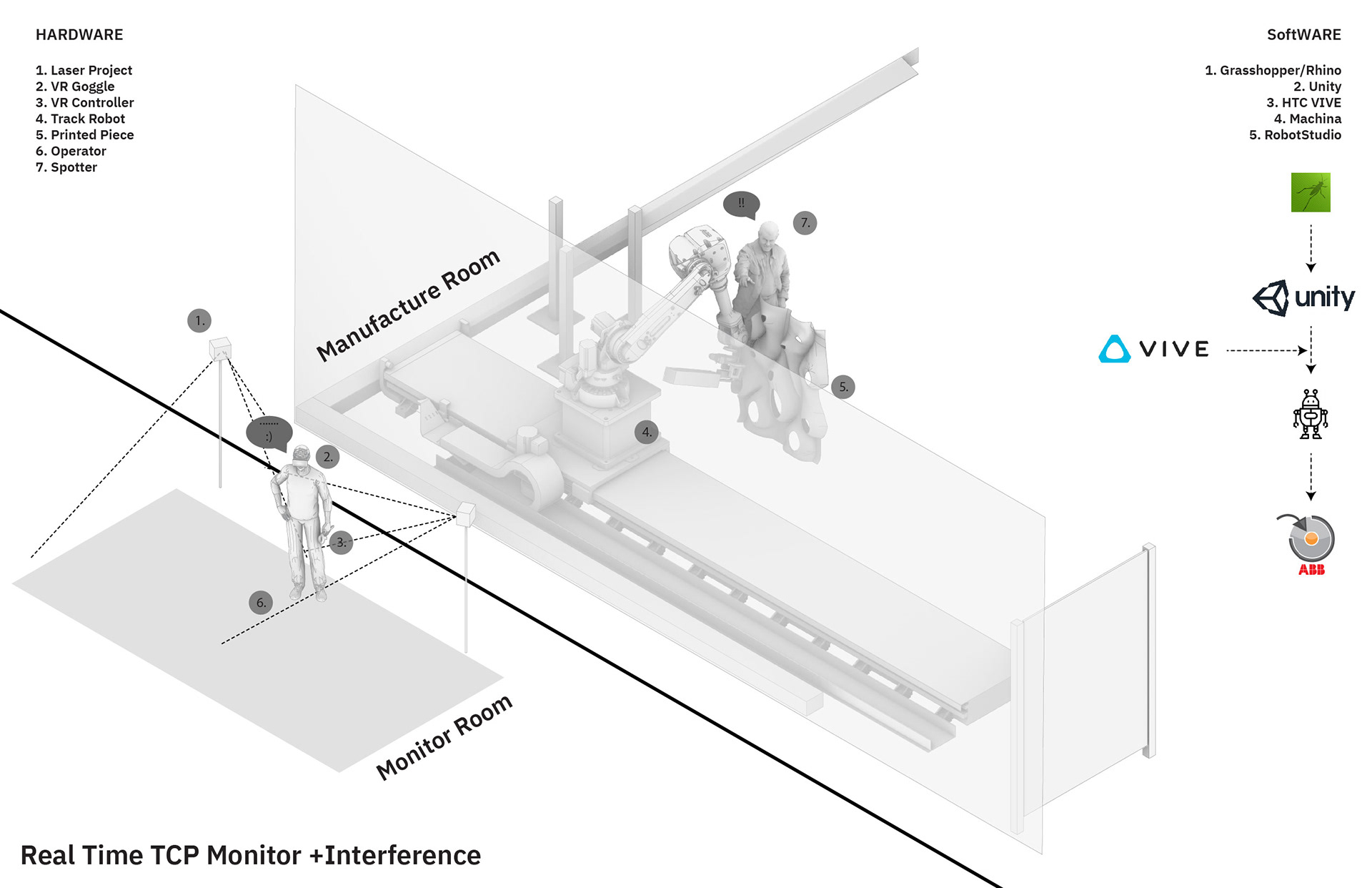
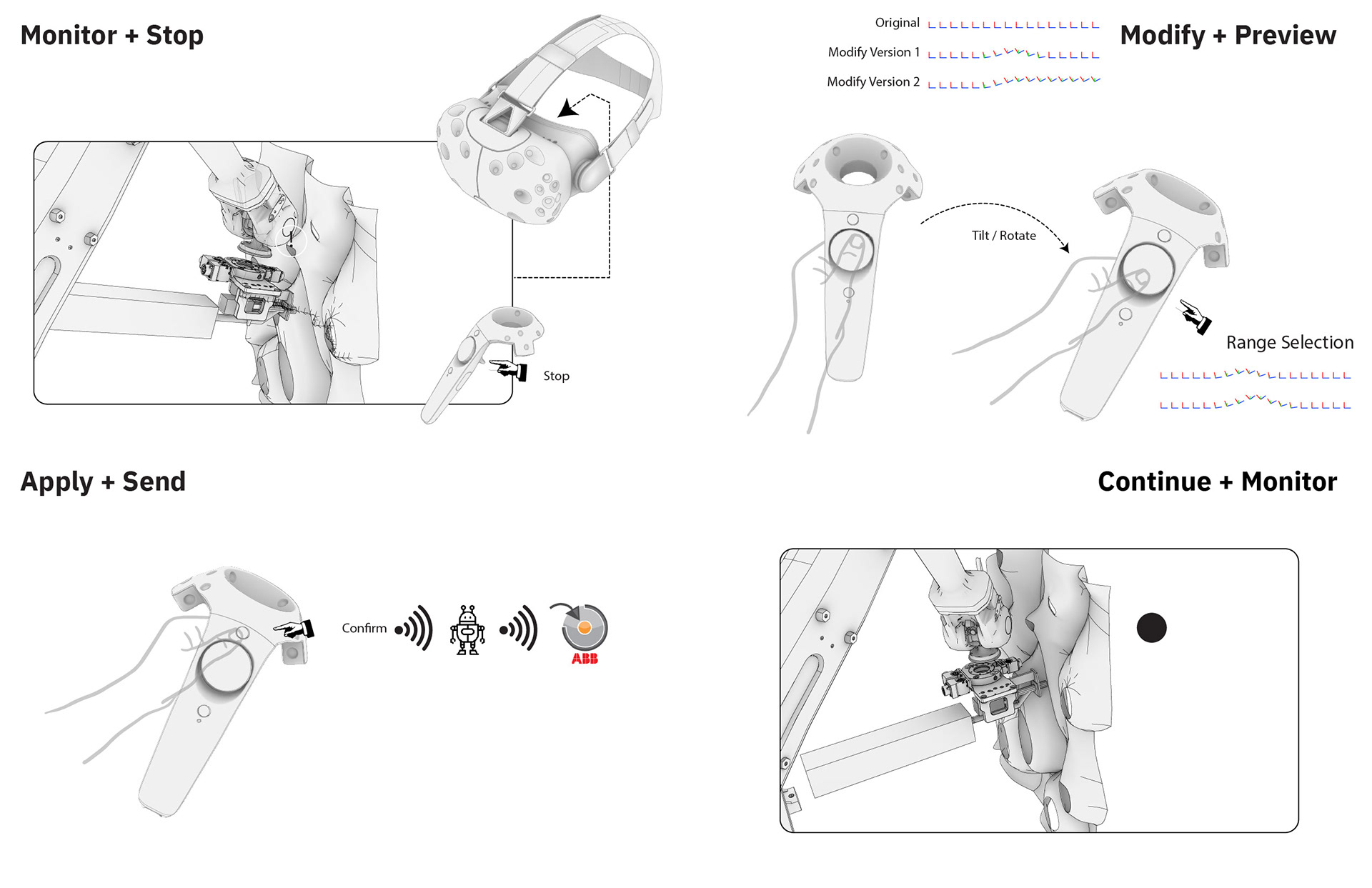
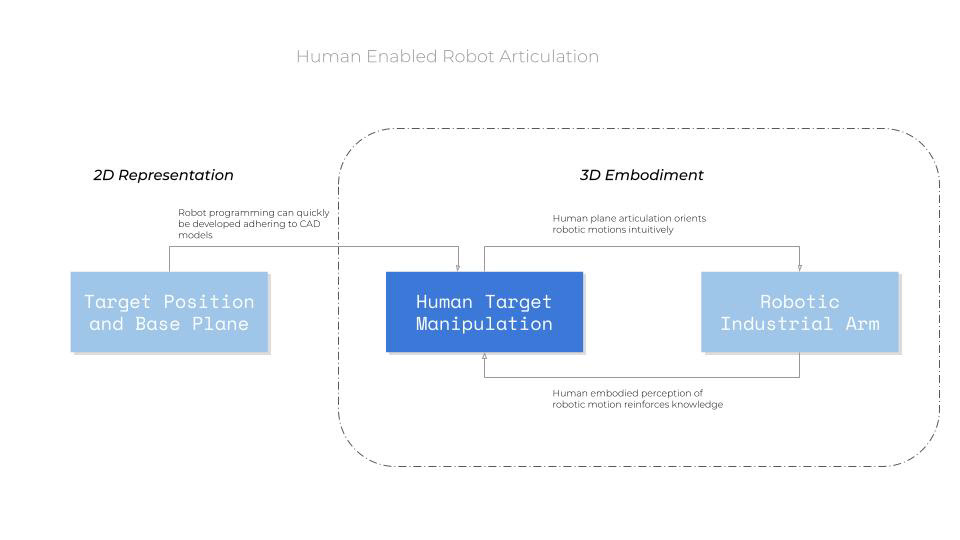
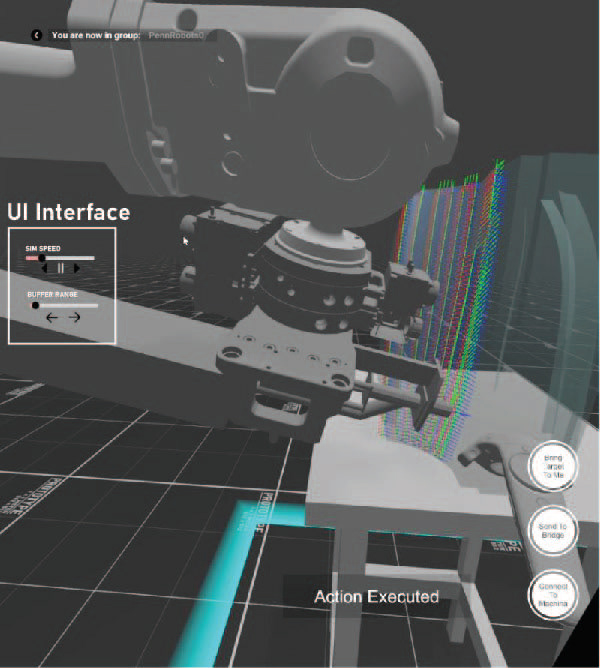
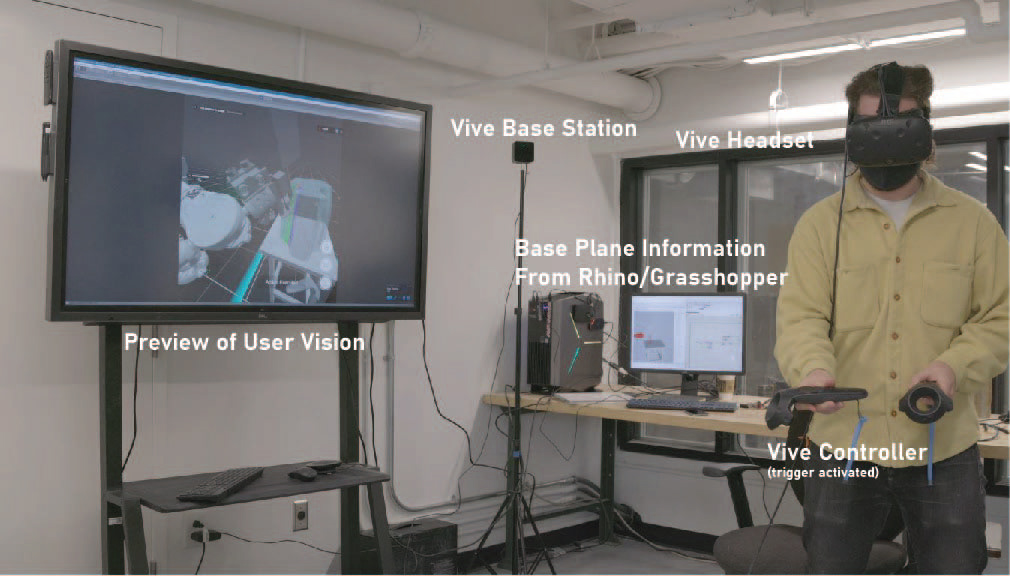
PHYSICAL TOOLS
The development of complex algorithmic and formal designs necessitated equally complex physical tools and production processes. Without consideration of the tooling and material limitations of our lab we would never have been able to achieve a fully developed mock-up.
INDUSTRIALIZED SMEARING END EFFECTOR
Although the simple stainless steel ball tool we used for our experiments worked plenty well at the research level, we needed to better understand what an industrialized process might look like for robotic smearing. The next few pages show how the custom end effector could have a dynamic set of features to allow for tool changing and water-pass through.
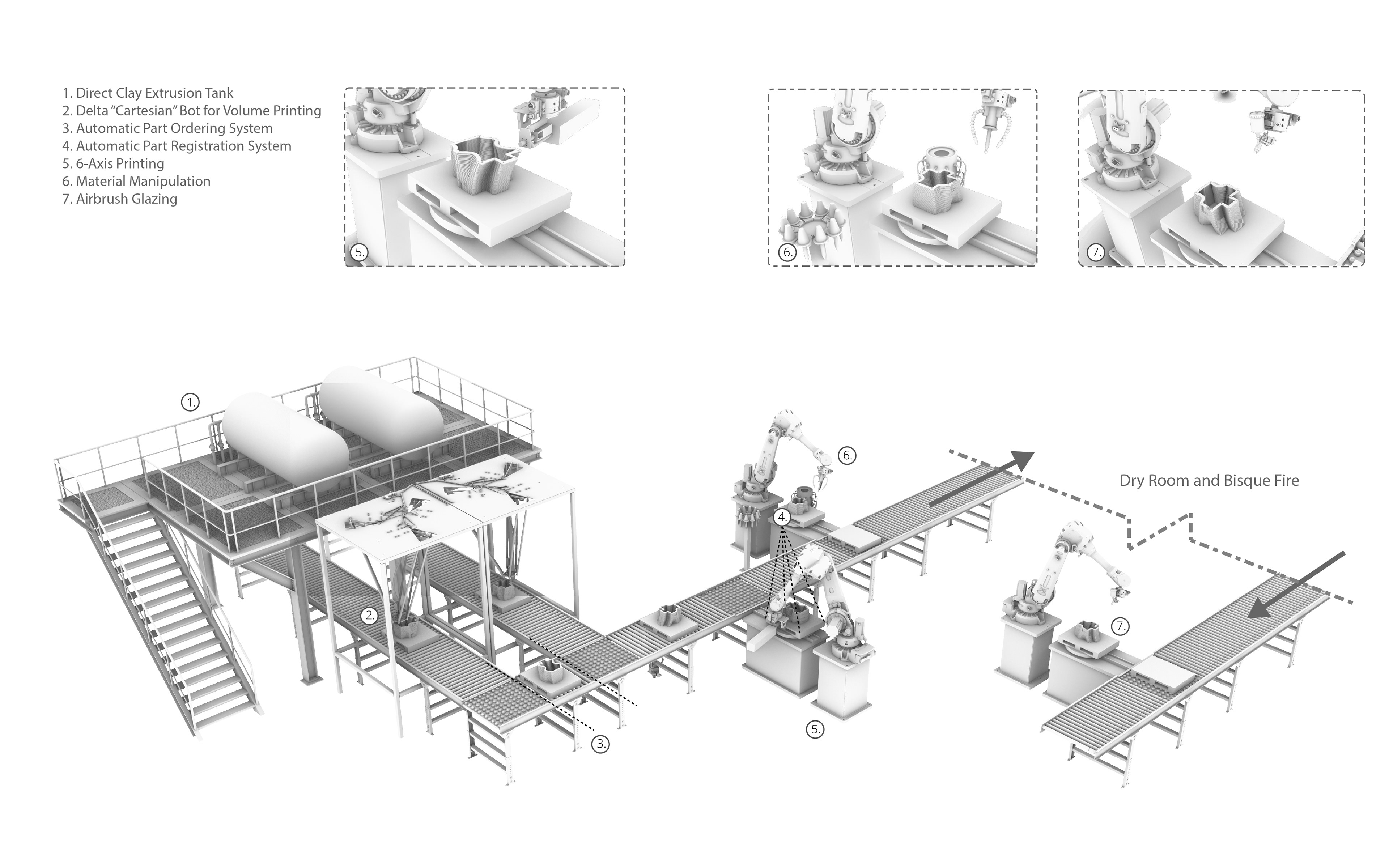
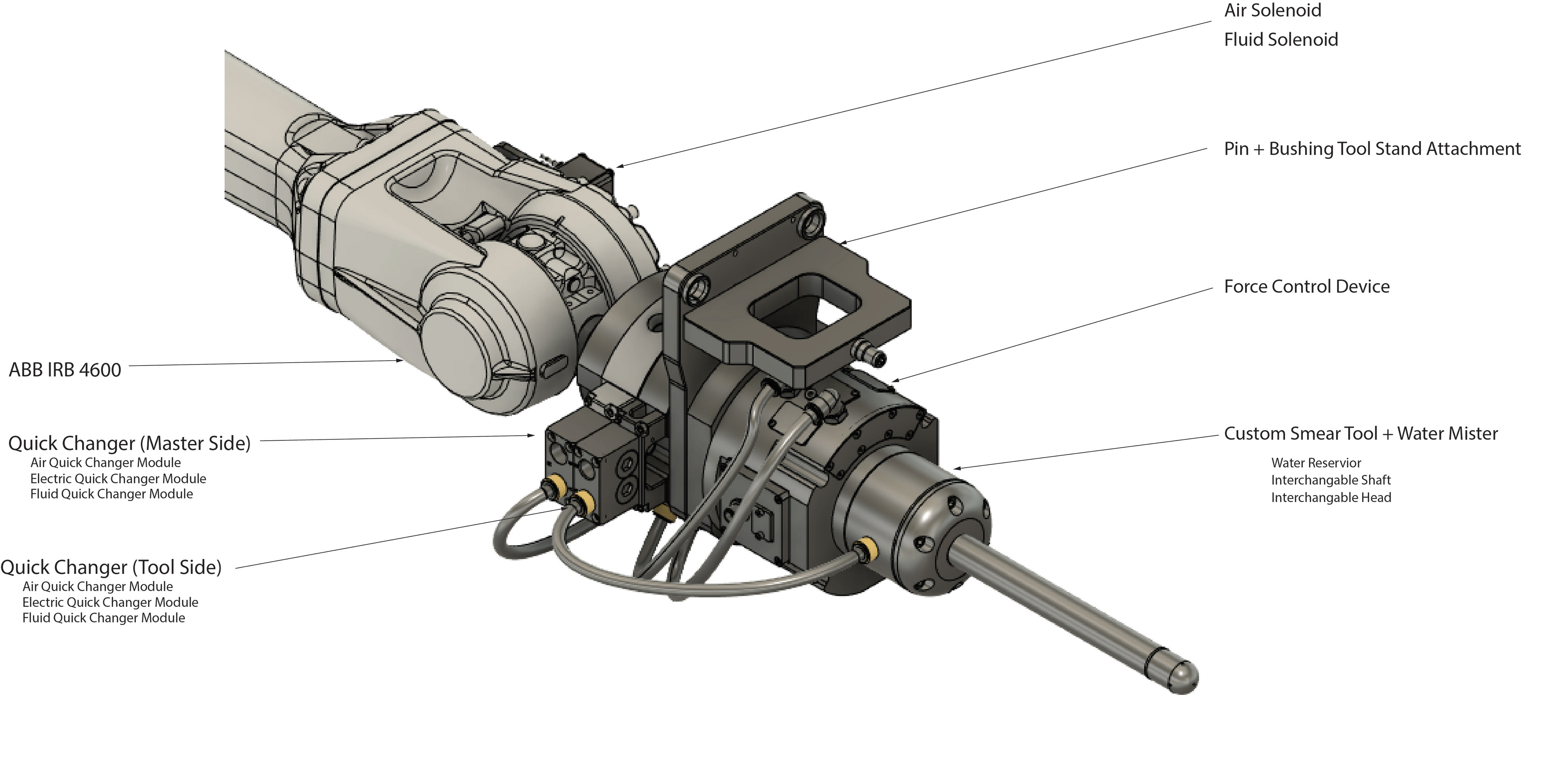
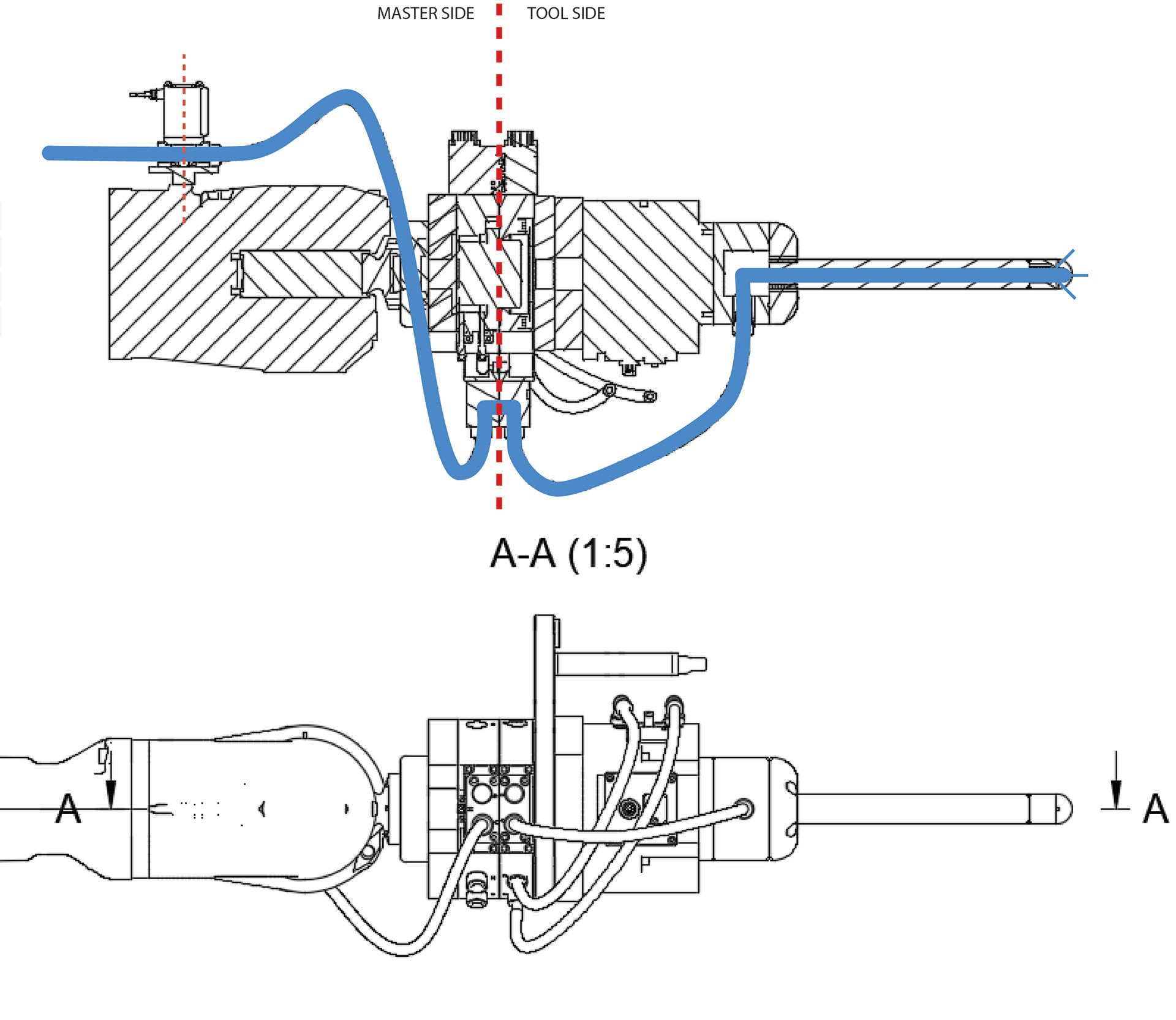
Full Scale Prototype
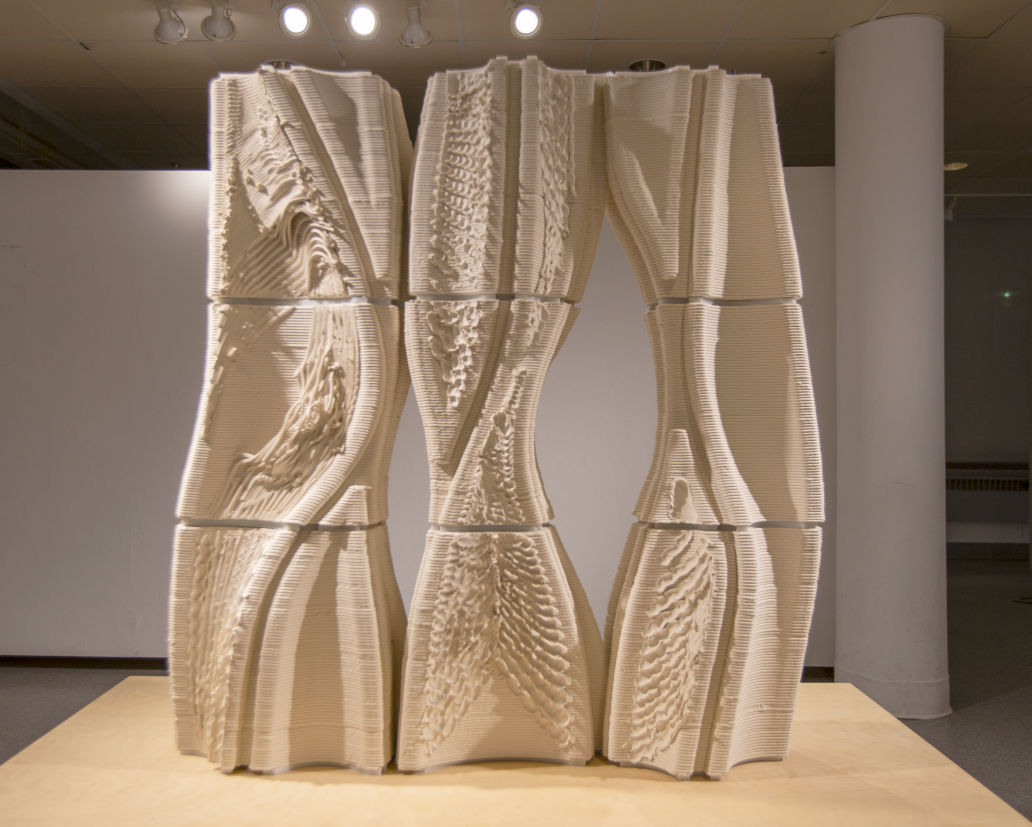
SURFACE MANIPULATED EXTRUSIONS AND RETOOLING [s.m.e.a.r.]
Surface Manipulated Extrusions and Retooling creates a controlled blending effect between the multiple extrusion layers. This process is both an aesthetic one, and one that we propose may increase layer bonding.
DELAMINATION
Influenced by the jumping cholla cactus, the vertical joints of our façade system delaminate to create apertures. With the potential to vary in scale to accommodate a variety of programmatic requirements. The geometry of the apertures are define by both material and production constraints.
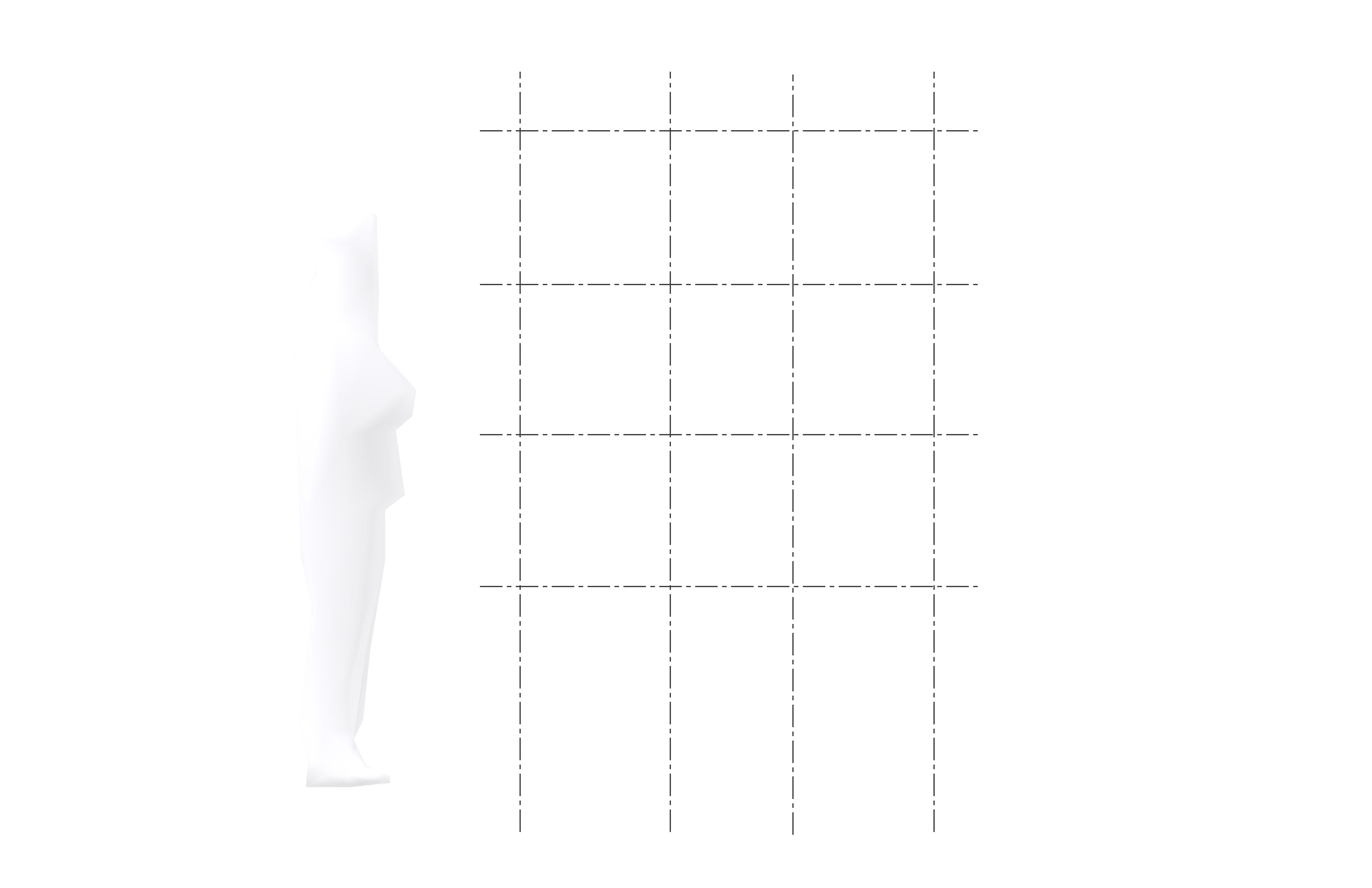
Initially conceived as a rectilinear grid
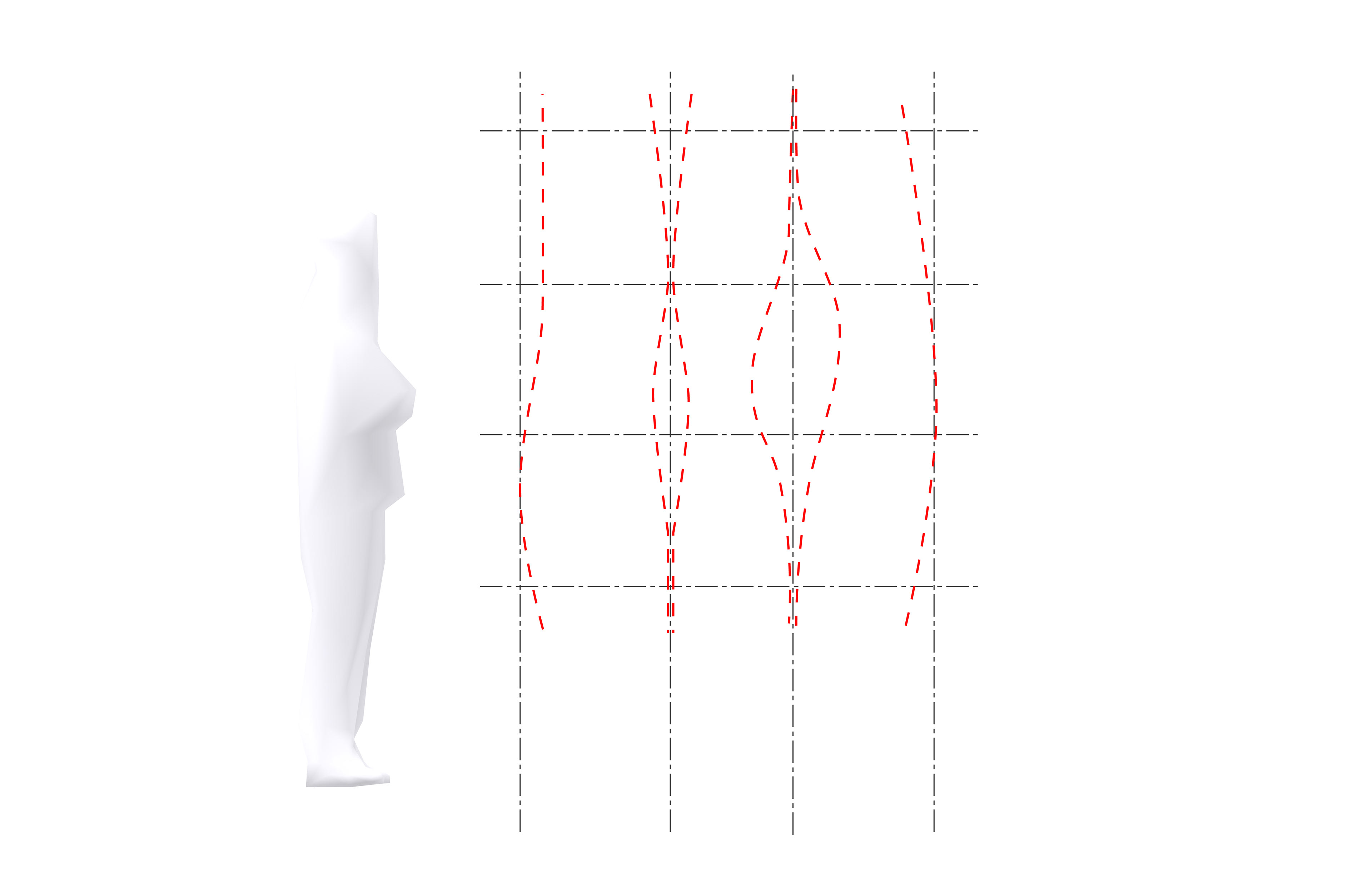
Vertical Joints are delaminated
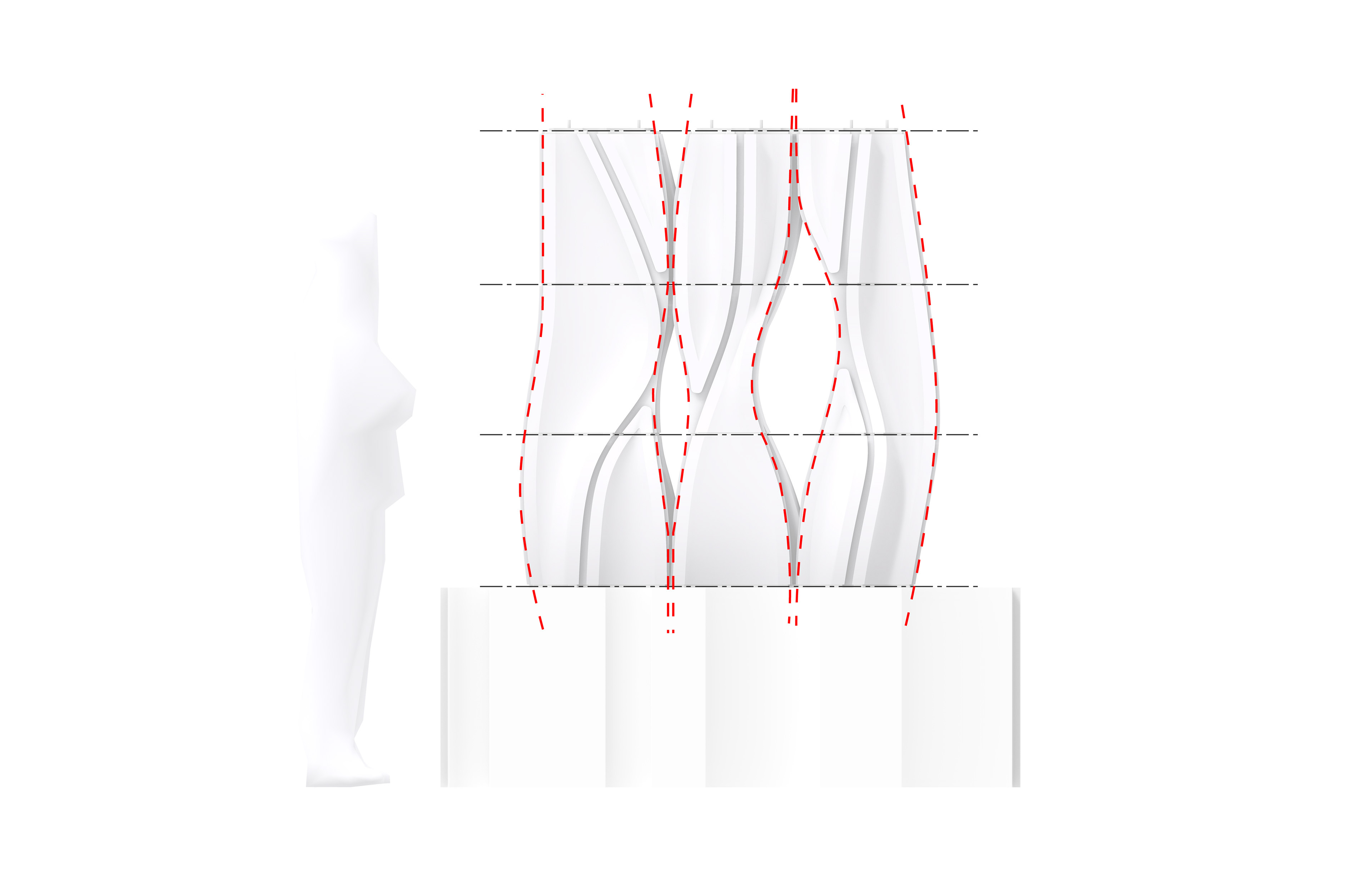
Delamination results in expressive geometry
STRUCTURE
Due to the requirement for the mockup to be have the ability to be re-assembled. A post-tensioned structural system was devised using HPDE spacers and threaded rods.
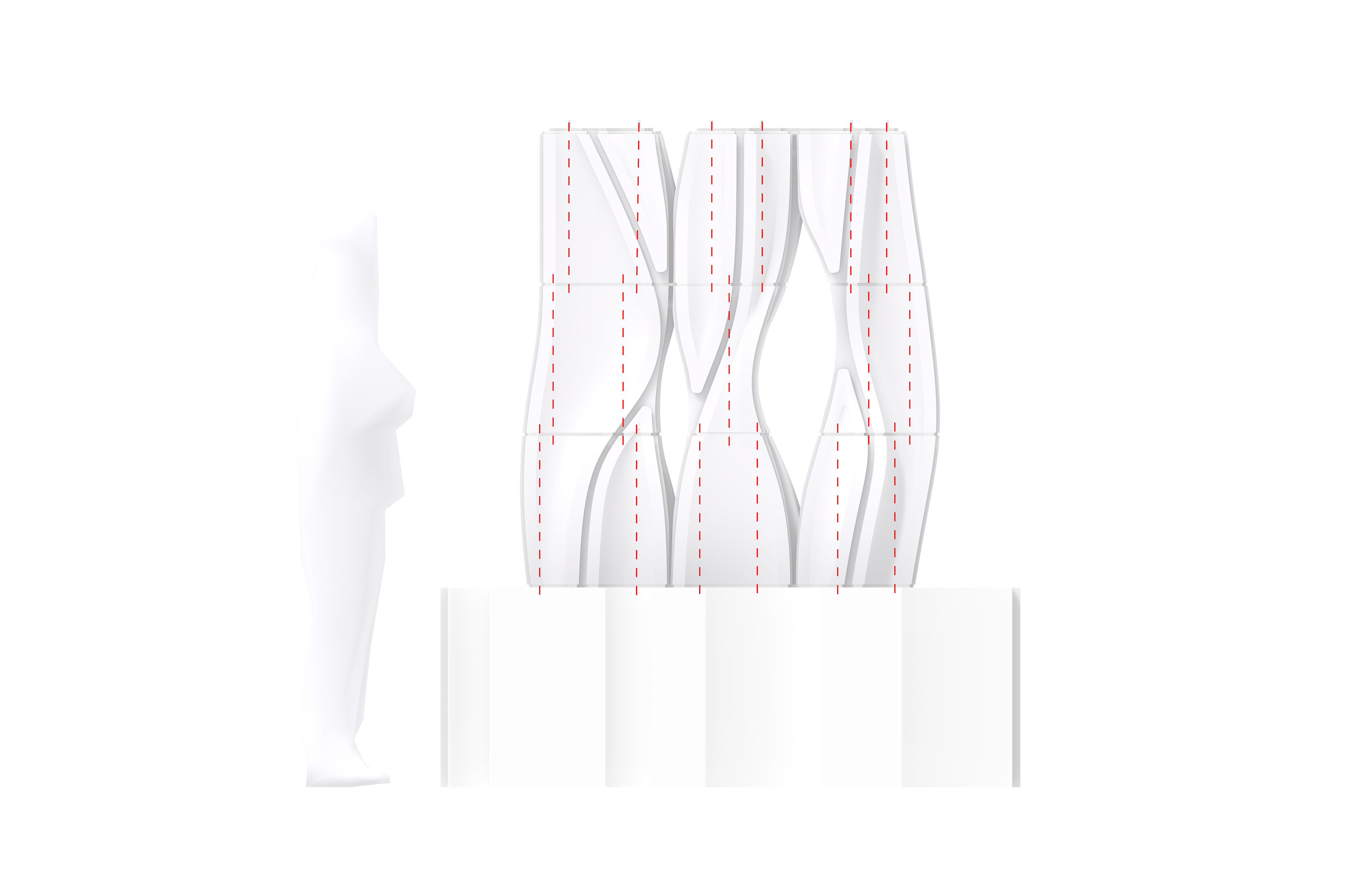
Vertical Structure - Post Tension Rods
![Horizontal Structure - HDPE Splice Plates [indicated by solid red line]](https://cdn.myportfolio.com/c1105dfb926cf7fd40cdd77b9c8bc71a/2f87bcda-94c3-4617-851e-8d94e6fa8aa0_rw_3840.jpg?h=c366a2cab4635f43422b899b10cbadb0)
Horizontal Structure - HDPE Splice Plates [indicated by solid red line]
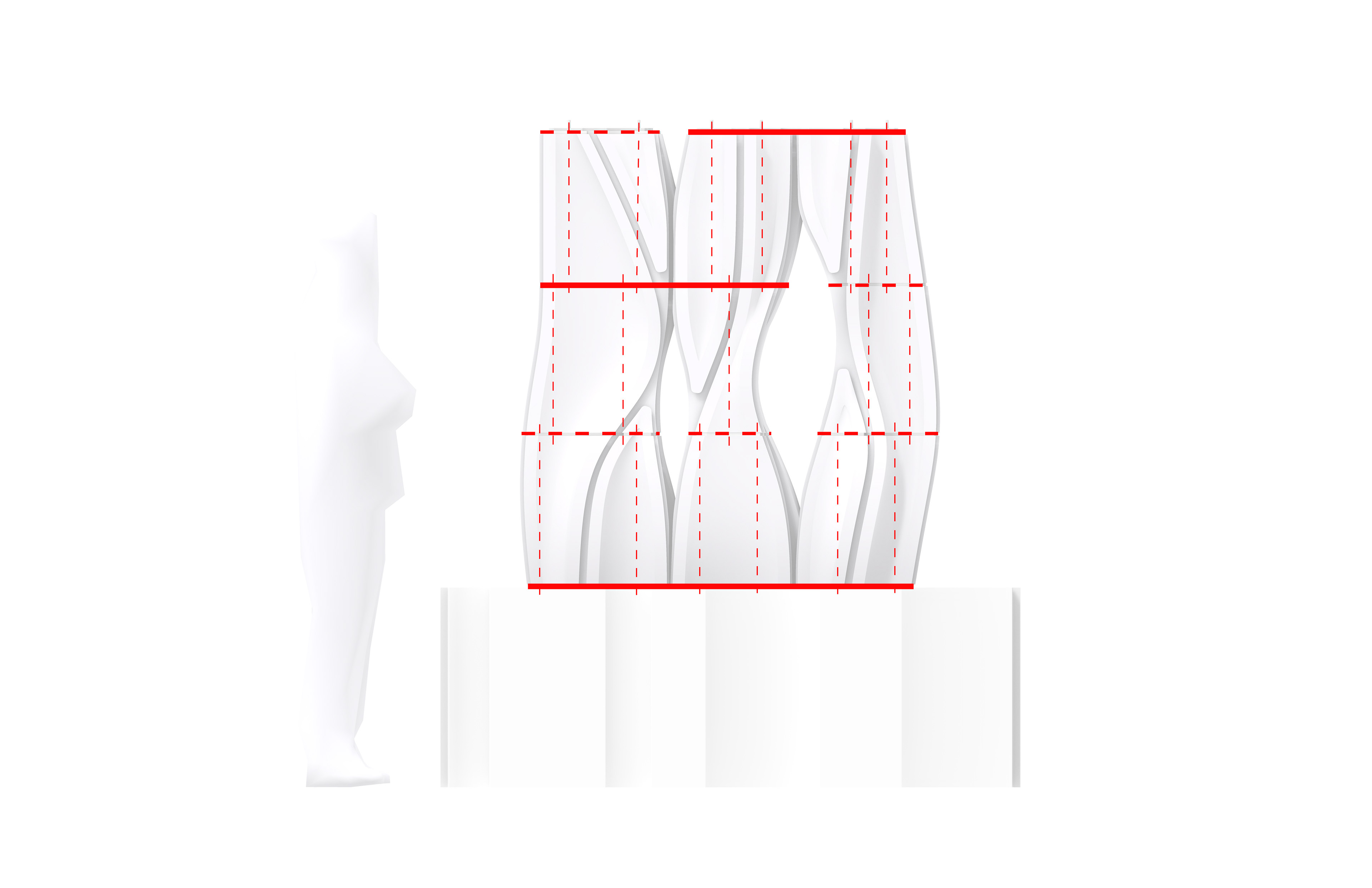
Overall Structure
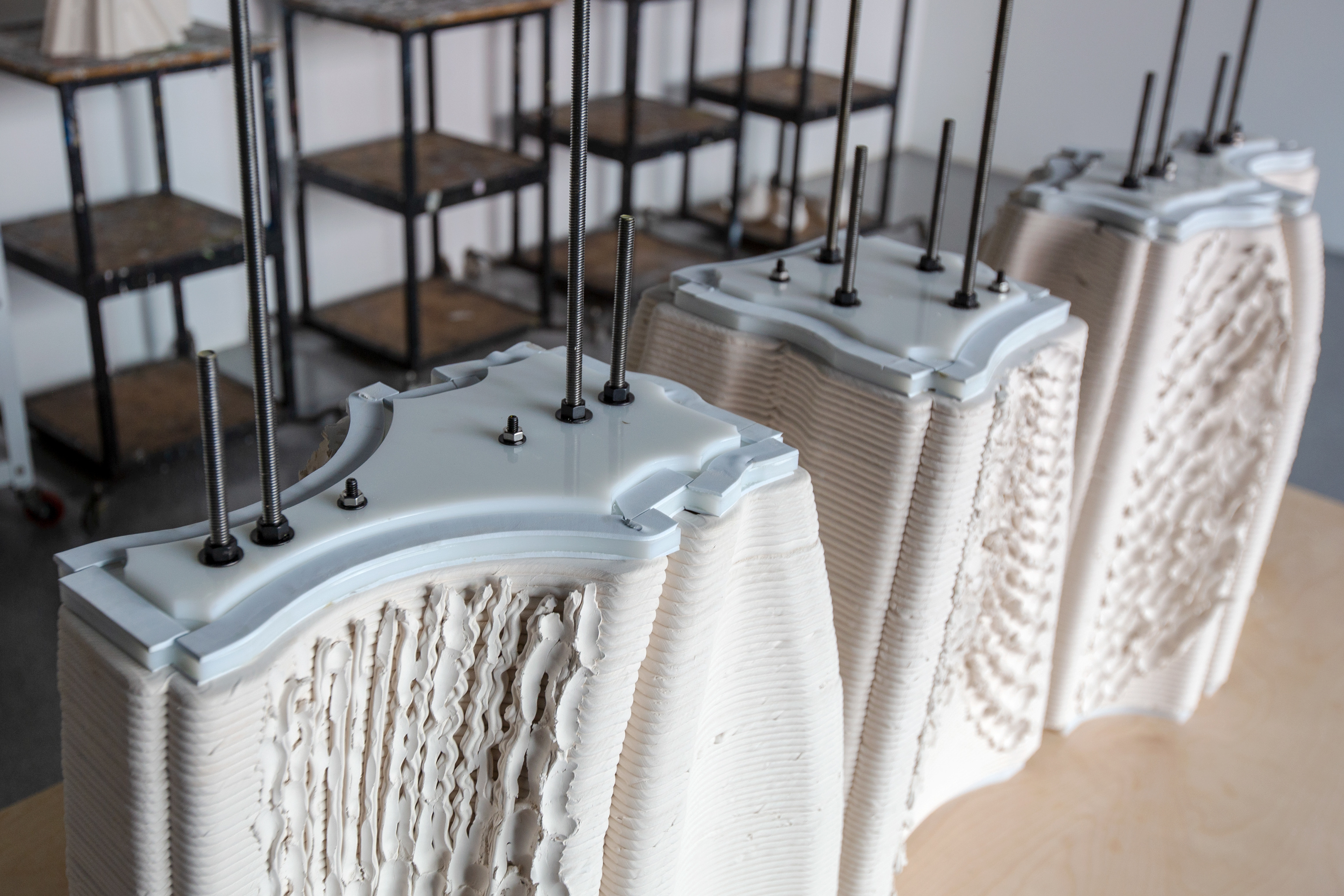
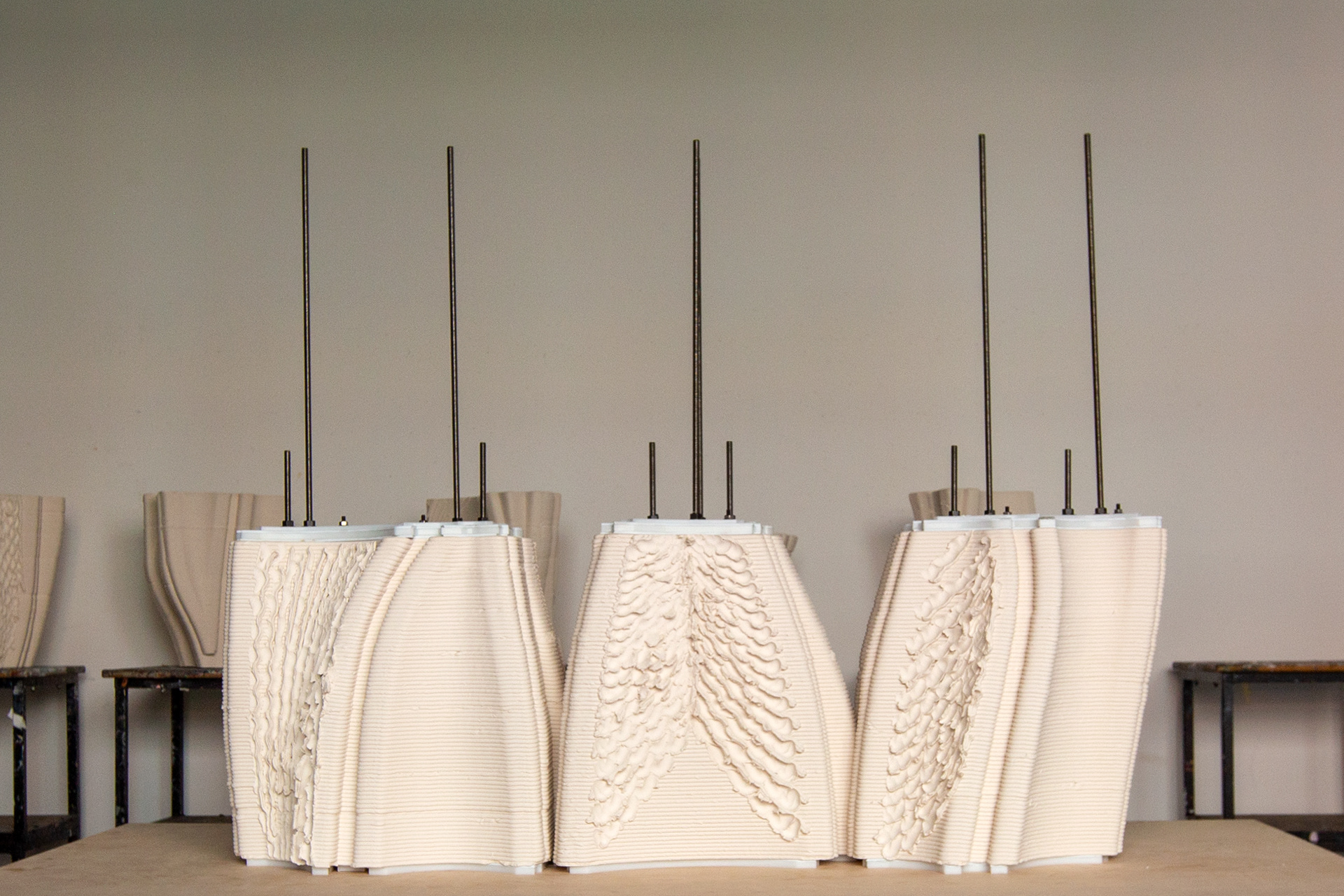
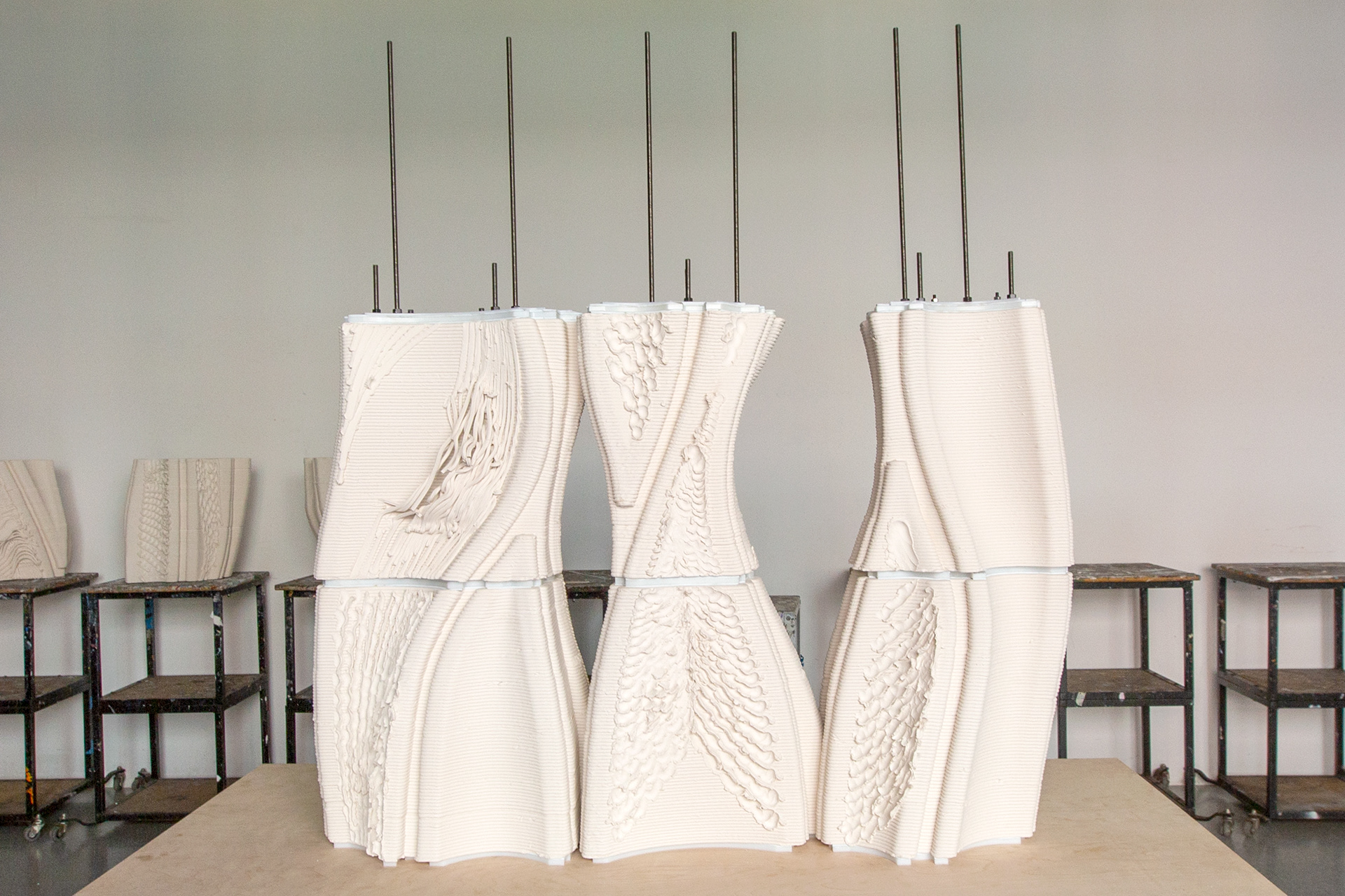
AGENTS
Agent based modeling is used to control how surface variation is layered onto the clay body. This surface variation ties together both a formal strategy for façade ornament, as well as creating secondary voids within the façade that enable bird inhabitation.
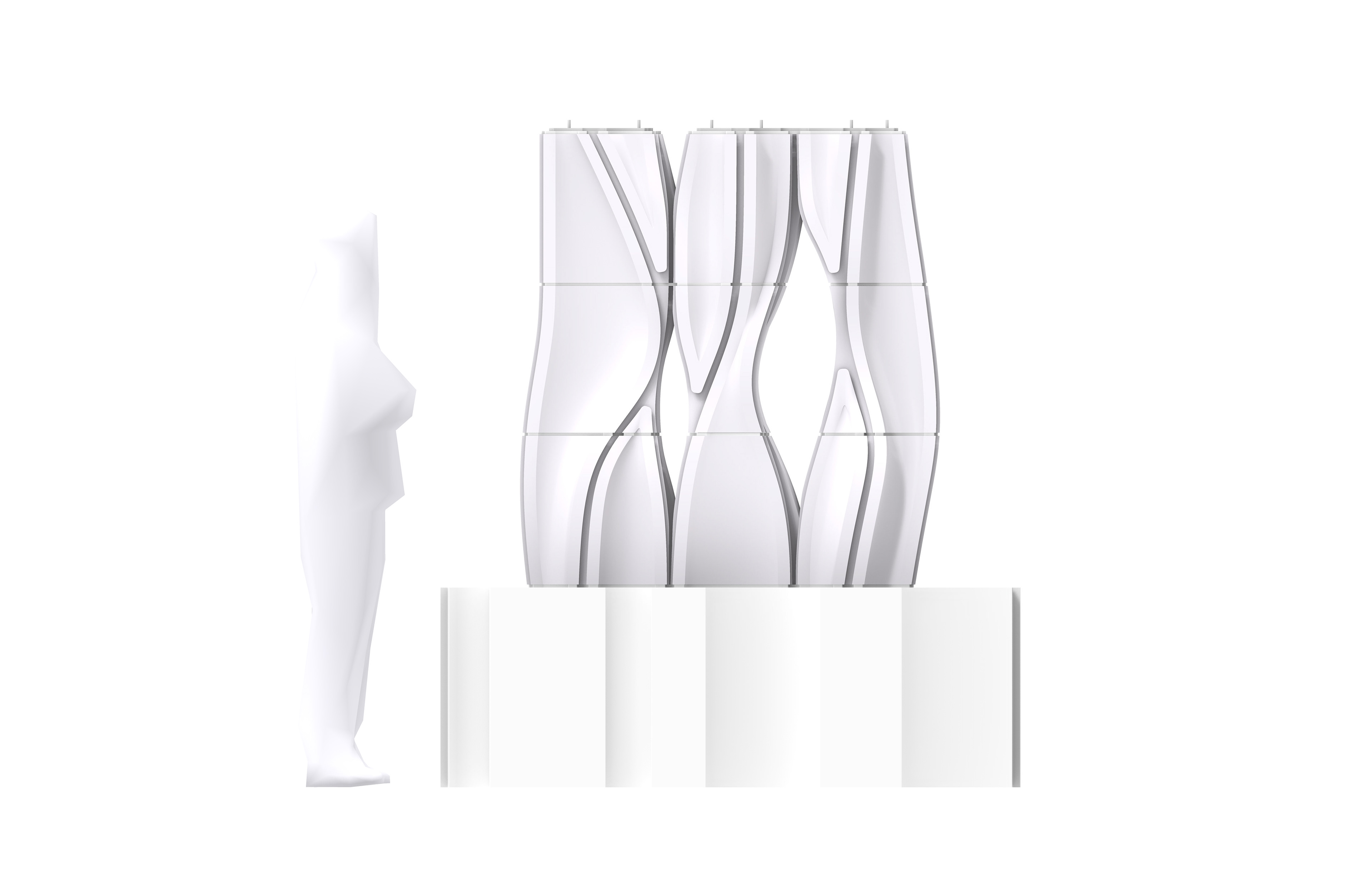
Base geometry created through 2.5D printing
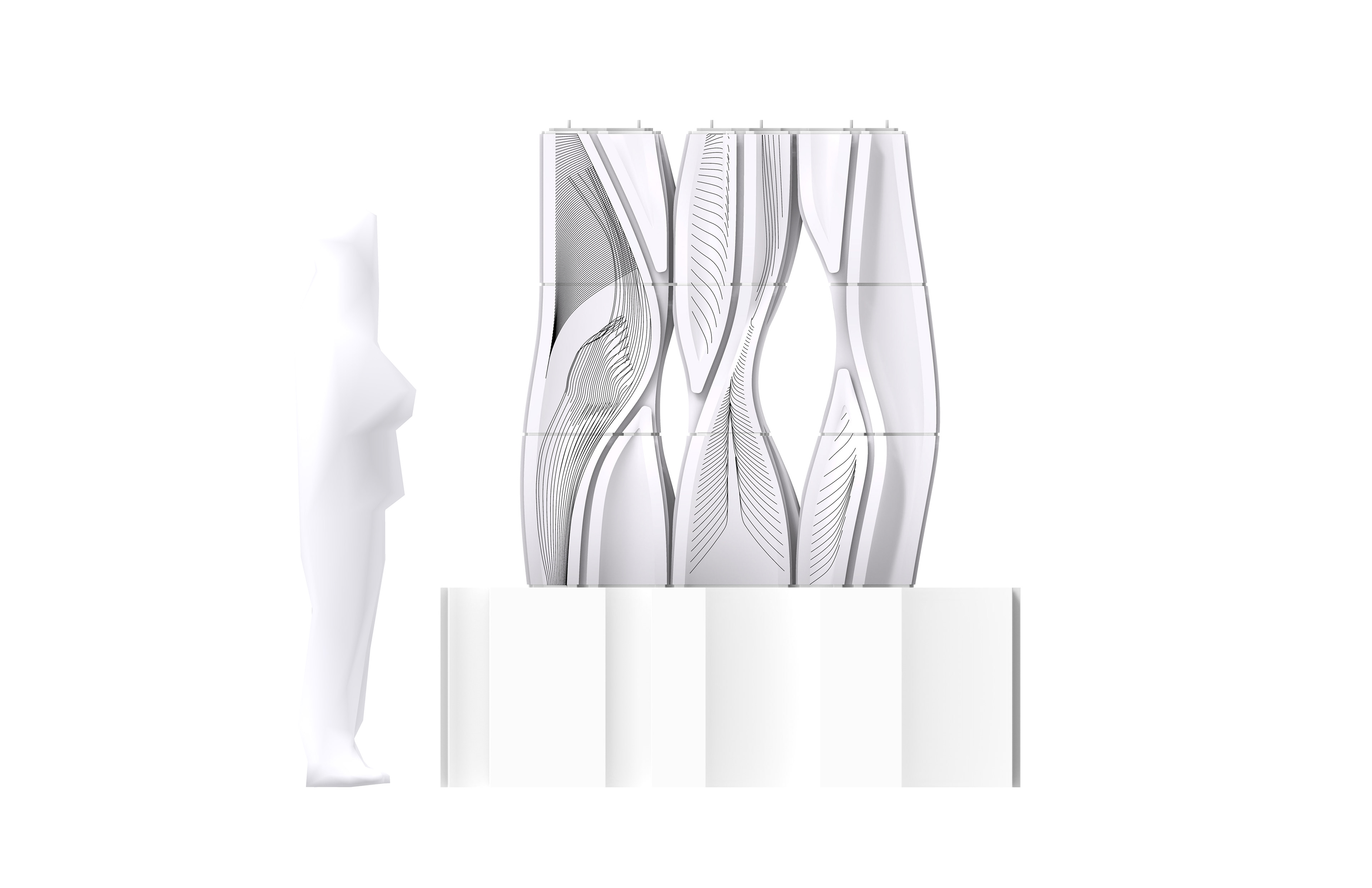
6-axis printing of agents
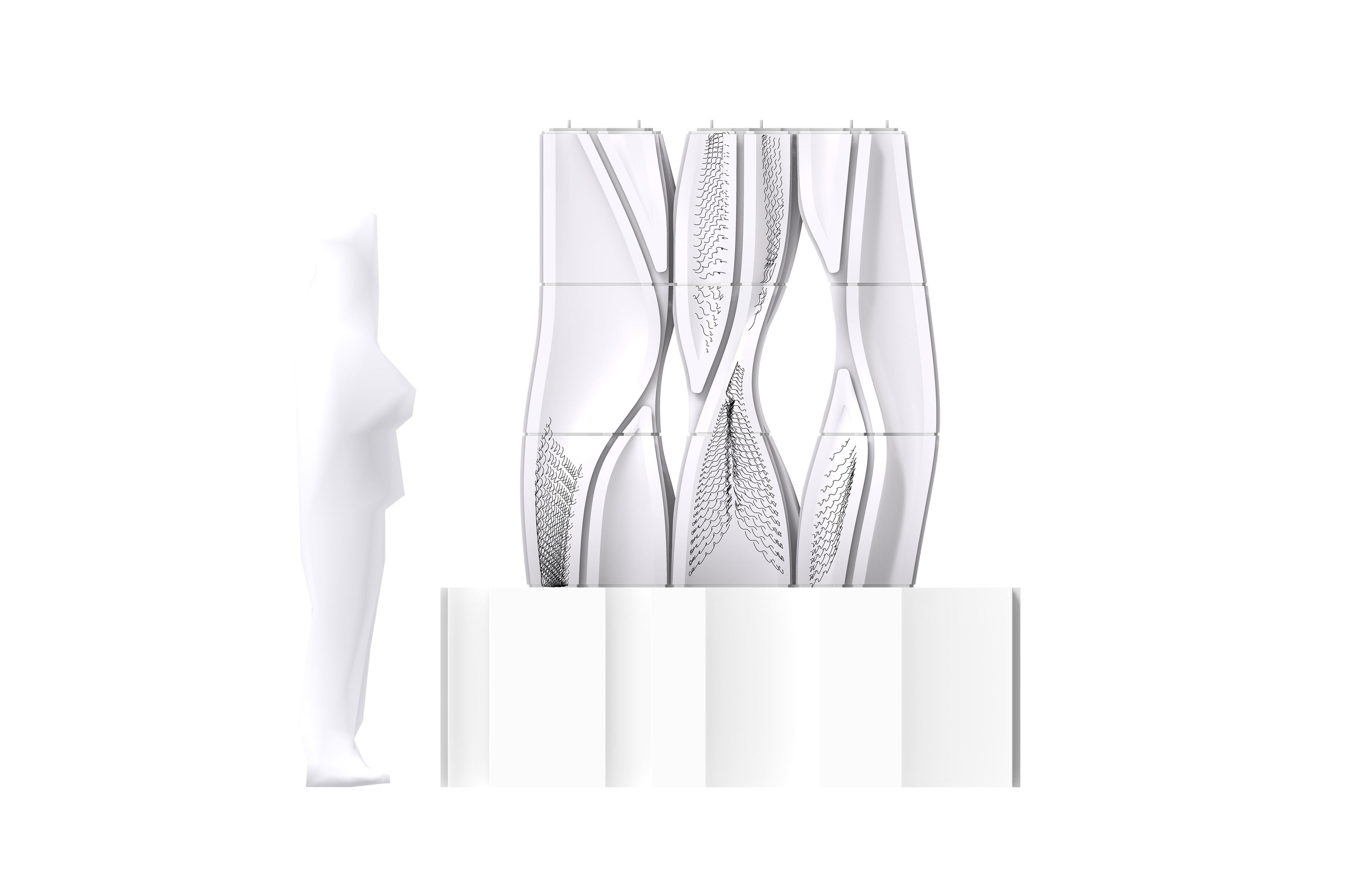
Using a custom end-effector, ornamentation was added. 6-axis robotic motion was influenced by agent curves
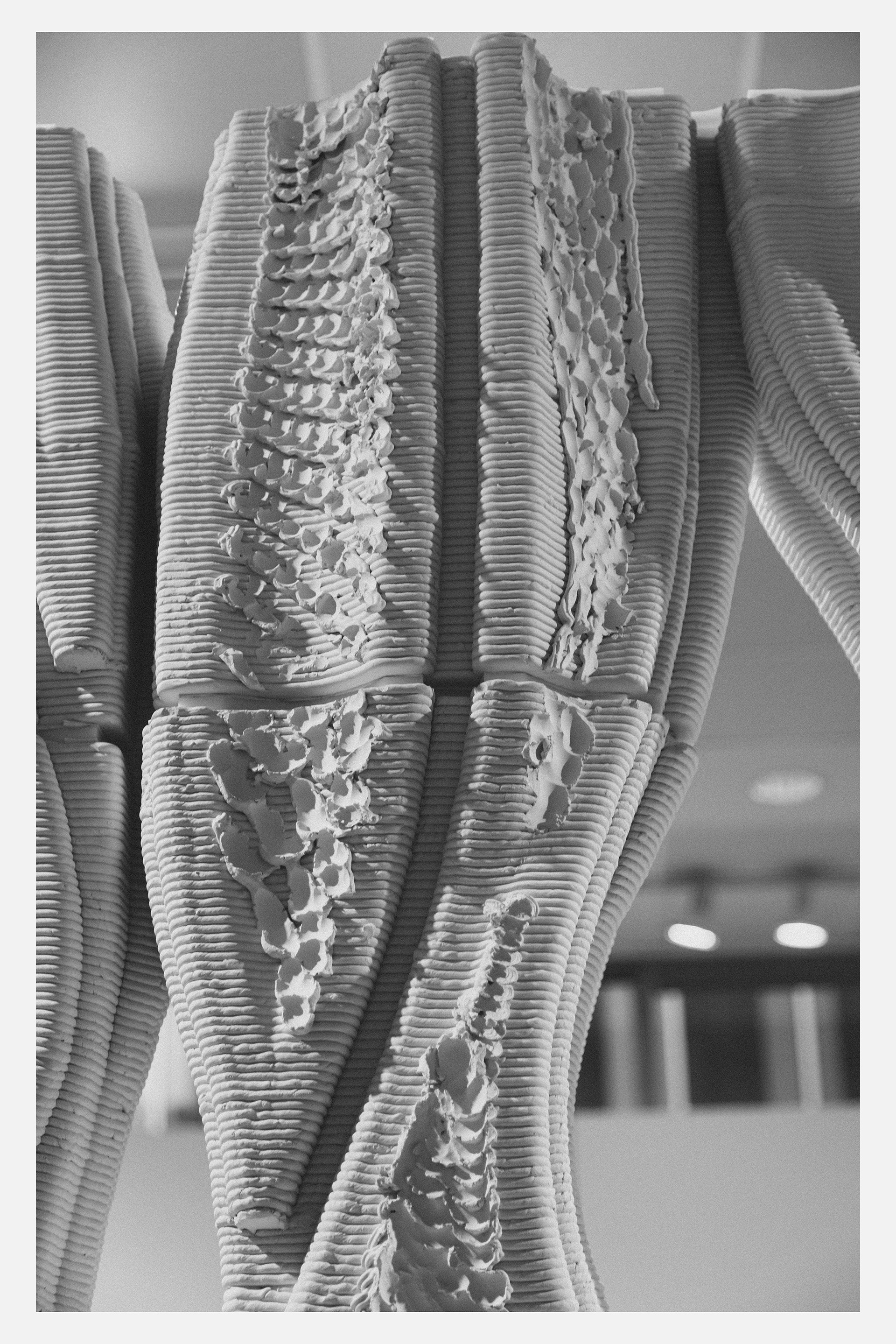
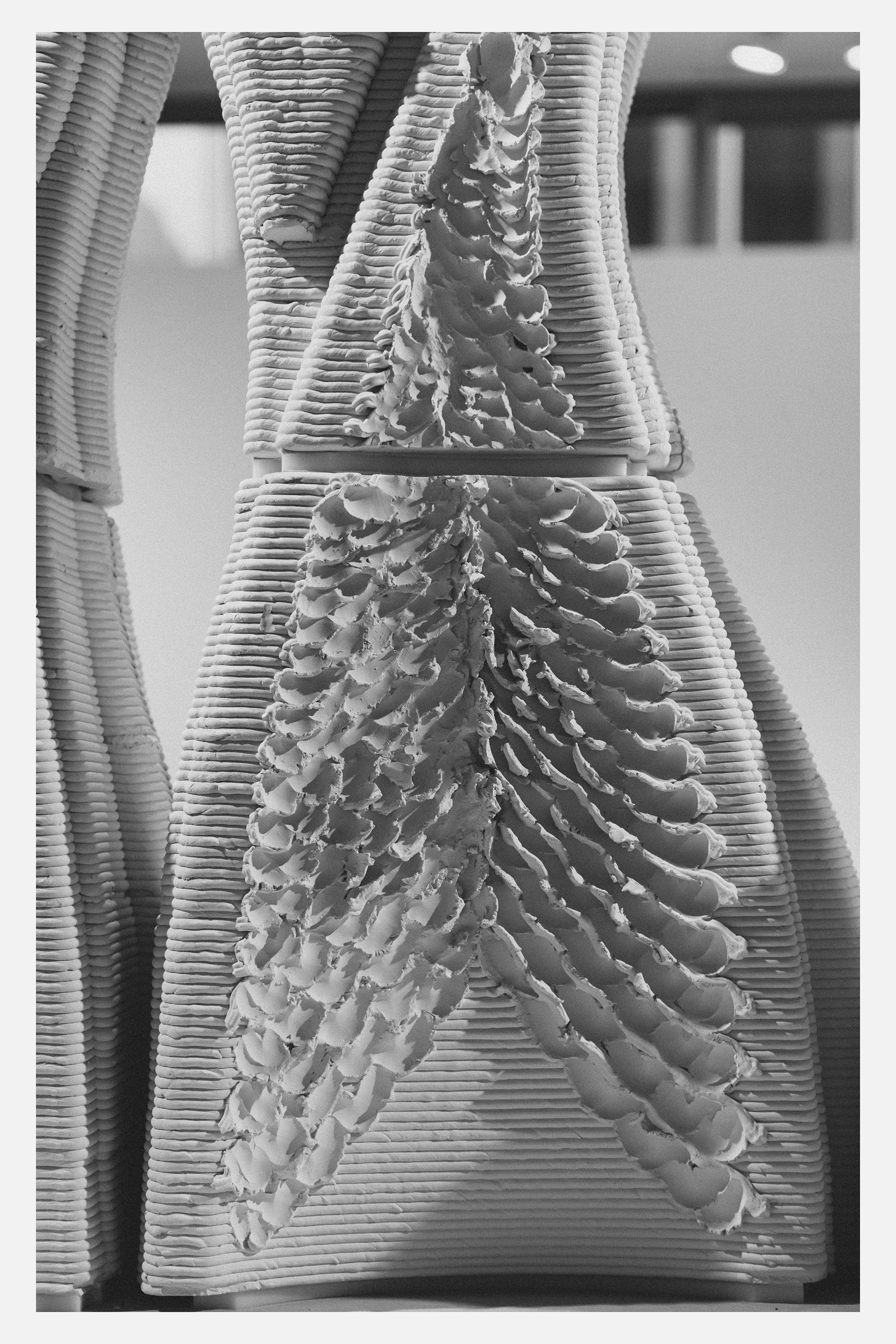
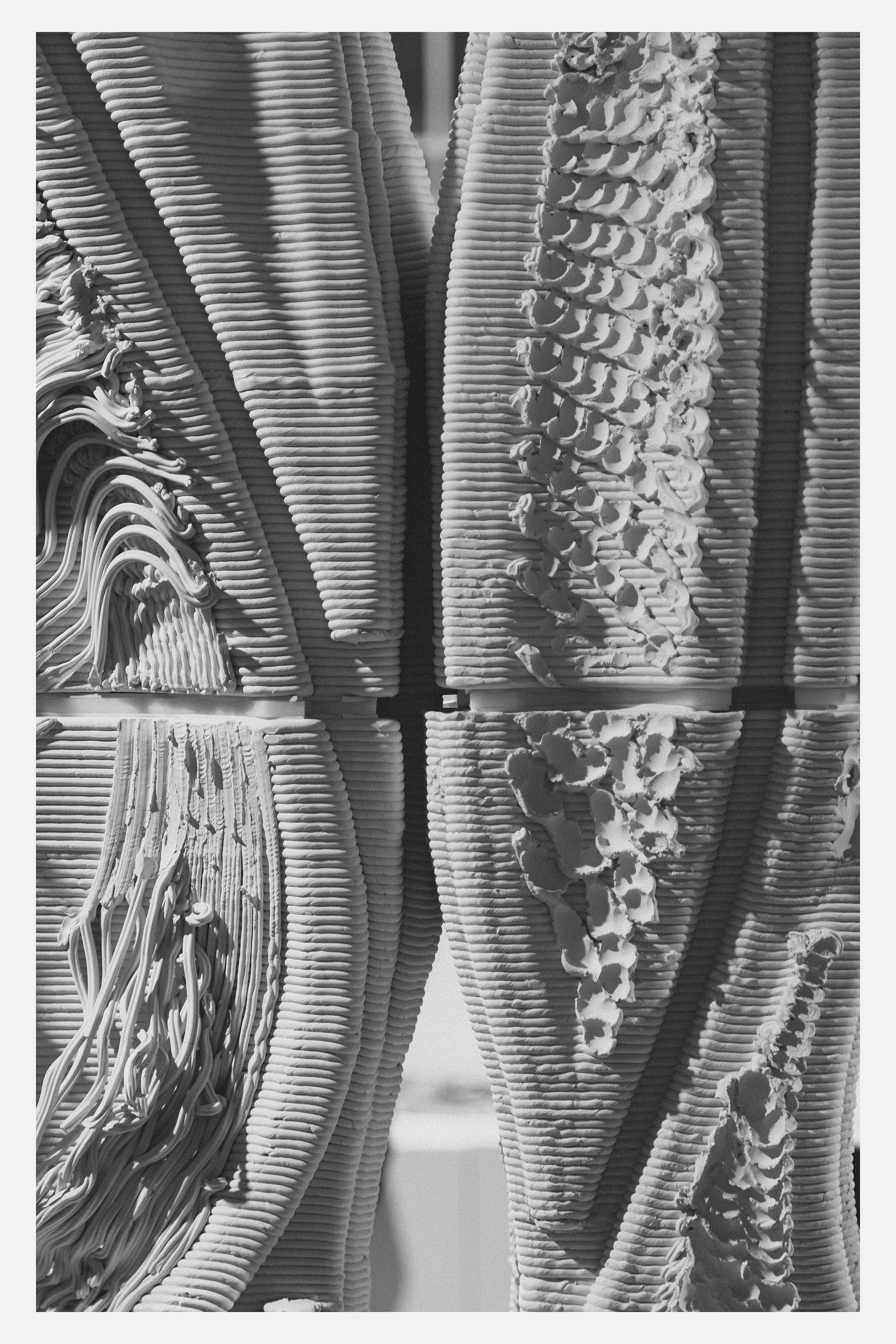
Weitzman School of Design
University of Pennsylvania
Spring 2021
802 Material Agencies
Partners: Jiansong Yuan + Grey Wartinger
Faculty: Robert Stuart-Smith and Patrick Danahy (TA)